Manufacturing Predictions for 2025
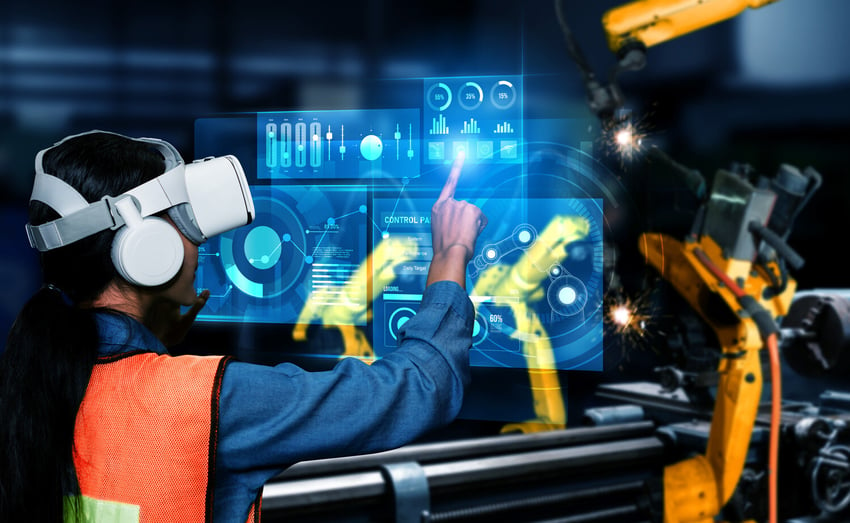
As 2025 kicks off, we're looking ahead to see that manufacturing is on the verge of a major transformation. As manufacturers ourselves, we keep our finger on the pulse of the industry and have been evaluating emerging trends to form key predictions that we think will shape the future of the sector.
The past few years have been a time of significant change for American manufacturers. They've faced economic uncertainty, rising costs, and a challenging business environment, but they've also made great strides in embracing digital technologies. This evolution, driven by Industry 4.0, is changing the way manufacturing works.
The rise of smart factories and automation
One of the biggest changes is the rise of smart factories and automation. According to a Deloitte survey, 98% of American manufacturers are already on the digital transformation journey. This shows their commitment to improving efficiency, cutting costs, innovating products, and giving customers a better experience.
Looking ahead, automation is set to increase significantly in American factories. By 2035, automation levels are expected to reach 79%, up from 69% today. Automation is no longer just about robots on the production line; it’s about creating interconnected systems that enable manufacturers to improve efficiency at every touchpoint.
Smart factories will leverage artificial intelligence (AI), machine learning (ML), and the Internet of Things (IoT) to create highly adaptive, self-optimizing production environments. These environments will not only reduce human error and downtime but also create new opportunities for predictive maintenance.
Automated Guided Vehicles (AGVs) are also becoming more popular in American manufacturing. They are expected to grow at a compound global annual growth rate (CAGR) of 14% over the next five years. Thanks to advances in AI and ML, AGVs are now smarter, more autonomous, and more efficient.
Among the various types of automated guided vehicles, tugger AGVs are predicted to dominate. Tugger AGVs are particularly effective at transporting heavy materials across production facilities, due to their ability to move multiple carts at once. This significantly enhances operational efficiency by consolidating multiple transport tasks into a single operation.
By reducing the number of individual trips required, tugger AGVs minimize traffic congestion within production facilities, optimize labor utilization, and decrease the overall transportation time. As factories become more interconnected, AGVs are set to be a significant contributor to the rise of automated production environments.
Predictive maintenance, in particular, will be a game-changer for manufacturers. By using sensors and data-driven automation, manufacturers can monitor equipment in real-time and detect potential issues before they become major problems. This will help reduce unscheduled downtimes, improve operational efficiency, and shrink maintenance costs. Through intelligent automation, factories will become increasingly resilient, reducing the risk of operational disruption.
Digital twins and the metaverse
Another exciting trend on the horizon is the use of digital twins and the metaverse in manufacturing. Digital twins (virtual replicas of physical assets or processes) will allow manufacturers to monitor and simulate their operations in real-time. In 2025, manufacturers will increasingly rely on metaverse-based tools to enhance employee training, perform virtual testing, and monitor factory performance from anywhere in the world.
The potential for virtual collaboration and remote diagnostics will reduce downtime, enhance decision-making, and offer more immersive experiences for both workers and customers. Deloitte’s report reveals that 29% of surveyed companies were already experimenting with digital twins and 3D modelling, with 20% having implemented across multiple projects or processes.
The metaverse is also expected to completely overhaul customer experience for manufacturing sectors. In the near future, we expect to see next-gen manufacturing capabilities integrated into customer experience hubs. These hubs will allow potential customers to experience products and production processes firsthand, bridging the gap between production and customer engagement in ways never before seen.
Sustainability and clean technology manufacturing
Sustainability is not just a buzzword; it’s a critical focus for manufacturers as they face growing pressure from customers, governments, and regulators to meet environmental, social, and governance (ESG) goals. We expect to see even greater investment in clean technology manufacturing, with companies prioritizing products and innovations that will help their customers meet emissions reduction targets and promote carbon neutrality.
Manufacturers will increasingly embrace sustainable production practices, such as energy-efficient systems, resource optimization, and waste reduction technologies. Many businesses are already reducing their reliance on diesel operated (or industrial combustion engine) material handling equipment, such as forklift trucks, and are instead opting for electric solutions.
By also leveraging advanced technologies like AI and machine learning, manufacturers can further enhance their sustainability efforts by optimizing energy consumption, reducing material waste, and improving overall production efficiency.
The role of AI and generative AI
Artificial intelligence (AI) will continue to play a key role in the transformation of manufacturing. AI is already embedded in industrial systems and this will only increase, driving operational efficiency and innovation. One of the most impactful uses of AI in manufacturing is the development of intelligent, adaptive systems that can autonomously adjust production processes in real-time.
For example, in highly specialized sectors like semiconductor manufacturing, precision is key. AI-driven systems will be able to continuously monitor and adjust production parameters to ensure optimal performance, reducing waste and improving product quality.
However, the growing reliance on AI also brings about important ethical considerations. Manufacturers must ensure transparency and accountability in AI-driven decision-making to maintain trust with customers and stakeholders. As AI becomes more embedded within manufacturing processes, it will be crucial for companies to implement frameworks that ensure fair and ethical use of AI technologies.
Addressing the skills gap
Despite the continued investment in automation and AI, the manufacturing sector still faces a significant talent gap, with 94% of executives acknowledging that there is a noticeable skills gap in US industry.
In the US, the number of unfilled jobs is expected to grow to 2.1 million by 2030. This could cost the US economy $1 trillion.
As technology becomes more sophisticated, there is a growing need for skilled workers in these high-tech environments. Manufacturers will need to continue developing long-term talent strategies for upskilling current employees and attracting new talent with expertise in digital technologies.
Despite these challenges, the US manufacturing industry is still investing in new equipment and facilities. For example, over $31 billion has been invested in clean-technology manufacturing facilities in 2024. This investment is expected to create close to 27,000 new jobs.
The US manufacturing industry is also working to address the skills gap. For example, the National Association of Manufacturers (NAM) has launched a number of initiatives to help workers get the skills they need to succeed in manufacturing careers.
In 2025, manufacturers will increasingly turn to advanced training programs and digital tools, such as augmented reality (AR) and virtual reality (VR), to provide employees with immersive, hands-on learning experiences to address the skills gap and ensure that workers are equipped to thrive in a digital-first manufacturing environment.
Employee safety is safeguarding future growth
Less of a trend for the manufacturing industry and more of a continued focus that is vital for manufacturers looking to future-proof their success, the importance of employee health and safety will only continue to increase. As businesses head into 2025 and beyond, the focus is shifting from reactive safety measures to proactive and data-driven solutions that not only protect workers but also enhance overall operational efficiency.
Wearable technology is allowing manufacturers to monitor employee health in real-time. By tracking factors such as movement, heart rate, and even posture, manufacturers can identify risks before they escalate such as detecting early signs of fatigue or exposure to unsafe handling practices.
Manufacturers are increasingly turning to mechanical and automated solutions to proactively reduce physical strain and improve safety. Electric tuggers, for example, allow workers to safely move heavy materials with little to no effort or strain, reducing the risk of manual handling injuries and improving operational efficiency.
An increasing number of businesses are looking to go 'forklift free', with retail orders of lift trucks down by 28% - the biggest decline annually for 14 years - leading many companies to turn to alternative material handling solutions such as electric tuggers. With no costly and time-consuming operator licenses required, electric tuggers mean anyone within the site can safely move loads.
Electric tugs provide a safe, efficient, and versatile solution for moving heavy loads, eliminating the tipping risks associated with forklifts and offering superior visibility and operator control. They require no license to operate and are suitable for a wide range of applications, from small carts to large trailers, making them ideal for manufacturers transporting heavy or diverse loads.
The move to implement more forklift-free areas and segregate forklifts from pedestrian zones is a trend set to continue for manufacturing in particular, as businesses turn their focus on maximizing staff safety.
Ready for the future of manufacturing?
The manufacturing sector is set to continue evolving at a rapid pace. The growing adoption of automation, AI, and digital technologies will enable manufacturers to improve operational efficiency, reduce costs, and stay competitive in an advancing global marketplace. At the same time, manufacturers will need to be placing their focus on workplace safety, sustainability, and talent development to ensure long-term success.
About the author
James Jones
With a Master of Engineering (Meng), James is our in-house automation and custom solutions expert. As Partner, James plays a pivotal role in driving the company's growth and development