The 10 Principles of Material Handling
Material Handling Principles
Material handling is an essential process in many industries and involves the movement, storage, control, and protection of materials and products throughout the manufacturing, warehousing, and distribution processes.
Thank you for submitting your consultation request.
A member of the team will be in touch shortly.
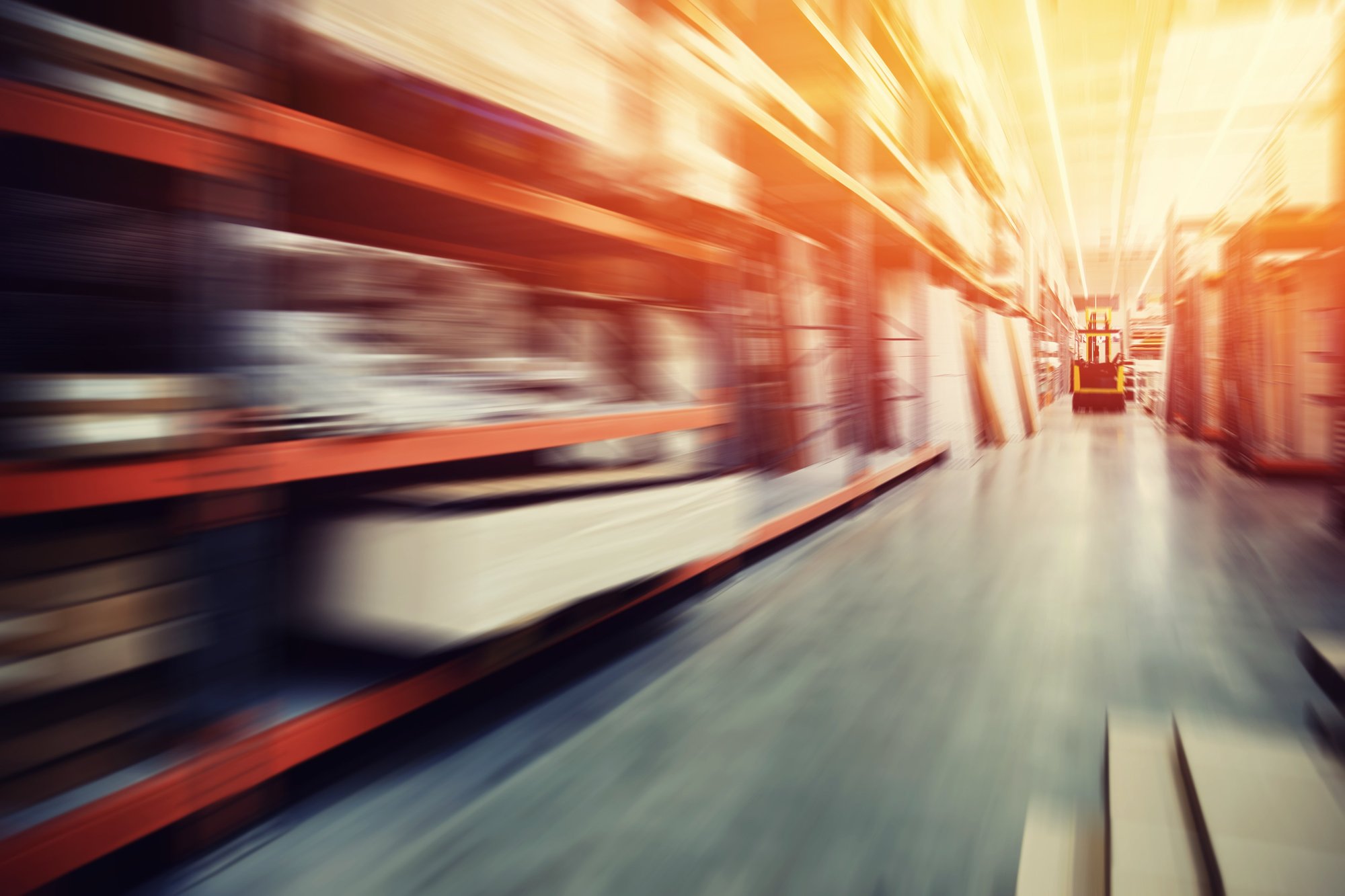
Guiding Principles of Material Handling
The goal of material handling operations is to improve efficiency, productivity, safety, and profitability while reducing costs and waste.
To achieve these goals, there are ten principles of material handling that everyone involved in the process should follow, whether reviewing existing methods or looking at new processes. They include:
Let's look at each of the principles of material handling, the questions you should ask yourself when assessing the movement of products, equipment, or raw materials, and what material handling equipment and material handling systems may be required.
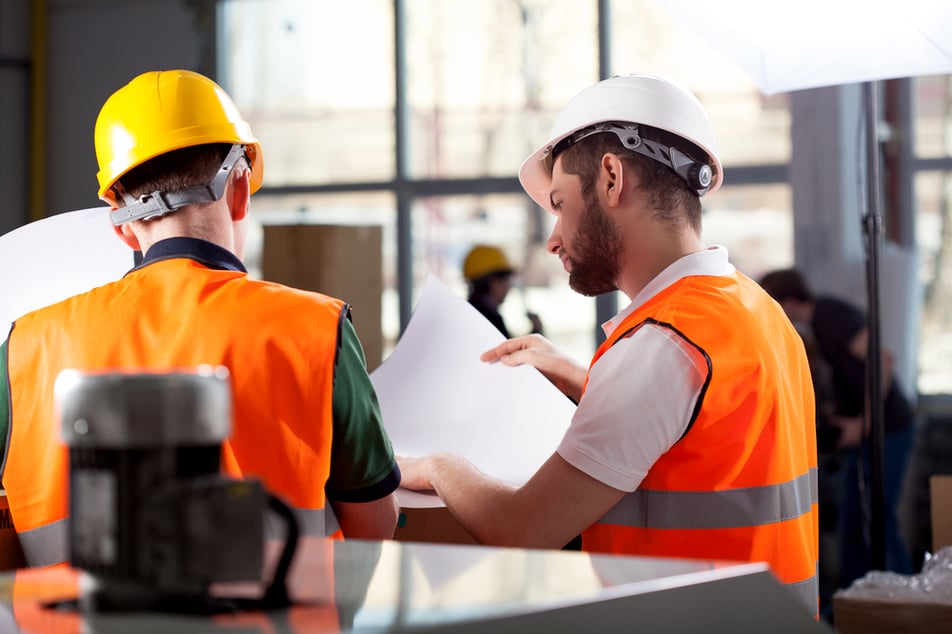
1. Planning
The planning principle involves identifying the materials that need to be moved, determining the best way to move them, and ensuring that the process is safe and efficient. When using the planning principle to assess a material handling task, ask yourself the following questions:
- What materials need to be moved?
- What is the best way to move the materials?
- How can the process be made safer and more efficient?
.jpg?width=952&height=674&name=agv-automotive-production_header%20(1).jpg)
2. Standardization
The standardization principle involves using the same processes and material handling equipment for similar tasks to reduce variability and improve efficiency. When considering standardization, ask yourself:
- Are there any similar tasks that can use the same processes and material handling equipment?
- Can standardization reduce variability and improve efficiency?
Our electric tuggers and tows are often used for a variety of load movement tasks, helping to drive standardization of material handling equipment and maximize efficiency.
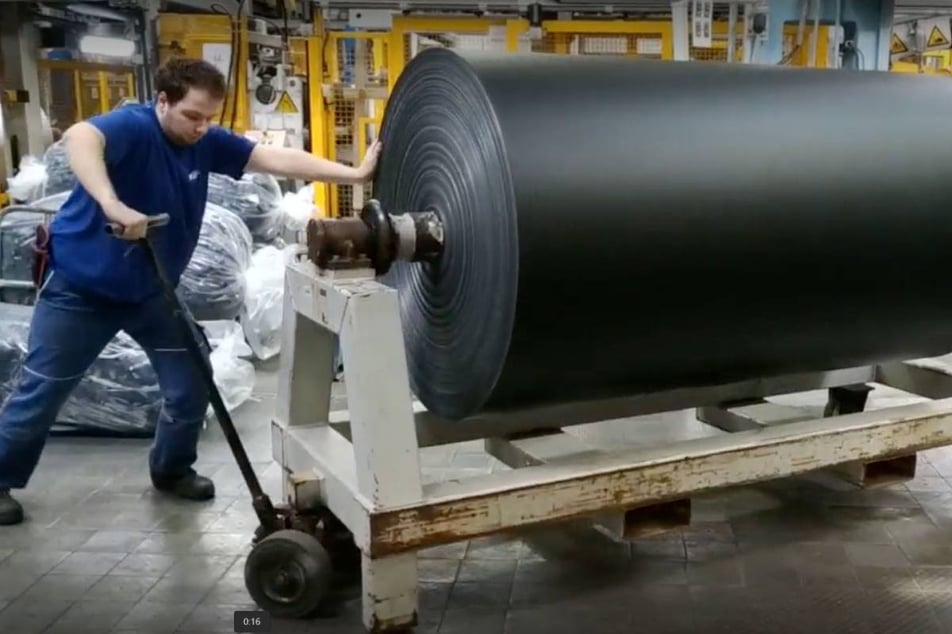
3. Work
This involves minimizing the amount of physical work required within material handling systems to move materials by using equipment and automation, rather than pushing the limits of human capabilities. When considering the work principle, ask yourself:
- Can equipment or automation reduce the physical work required?
- How can the process be made less physically demanding?
Putting stress and strain on people only creates risk, so reducing manual handling helps to protect the workforce, keeping them safe, but also empowers them to be more efficient.
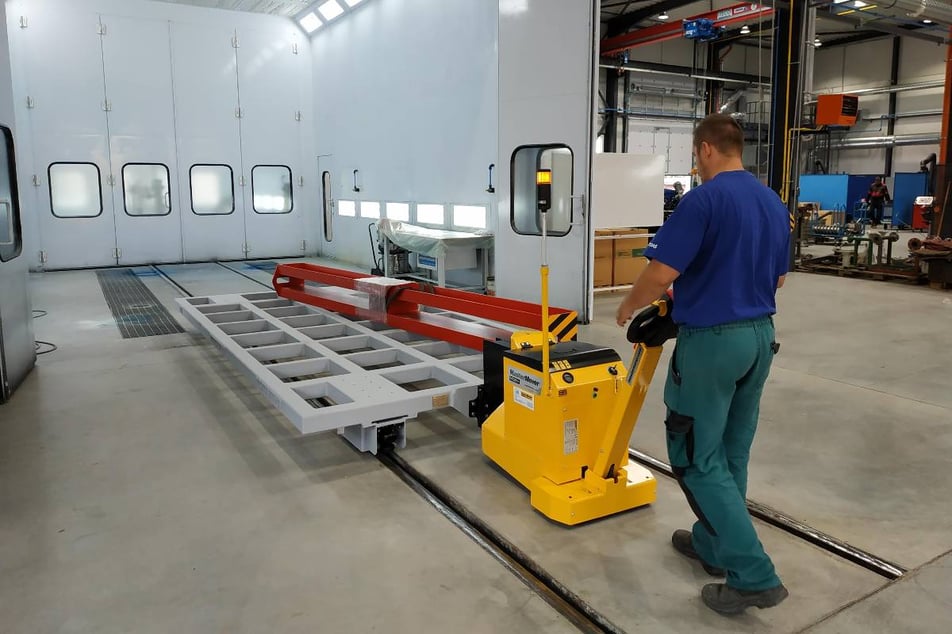
4. Ergonomics
The Ergonomic principle involves designing workstations and material handling equipment to minimize physical strain and fatigue. When considering ergonomics, ask yourself:
- Is the equipment designed to minimize physical strain and fatigue?
- Are workstations designed to minimize physical strain and fatigue?
The Ergonomic principle is one we pay close attention to at MasterMover, when designing material handling equipment, to ensure our electric tugs and tows are easy to use for safe and effective operations!
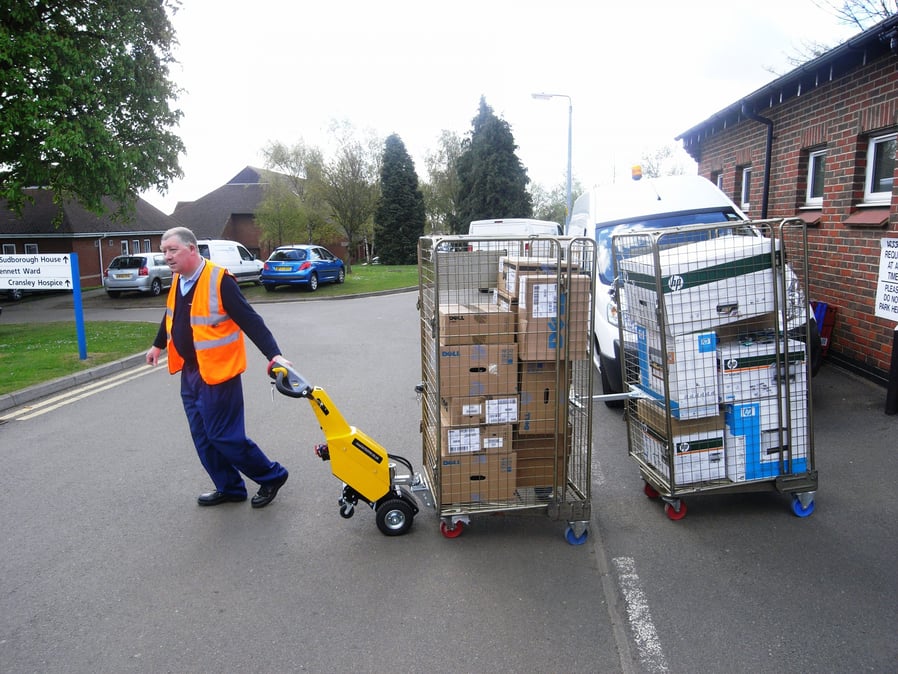
5. Unit Load
Looking at Unit loads involves consolidating materials into a single load for more efficient movement, to maximize physical material flow. When considering the unit load principle, ask yourself:
- Can materials be consolidated into a single load?
- Can unit loads be standardized for more efficient movement?
Trains of carts, platforms or dollies are often a good way to way to move more material in one go, reducing total trips or the number of times a task is carried out.
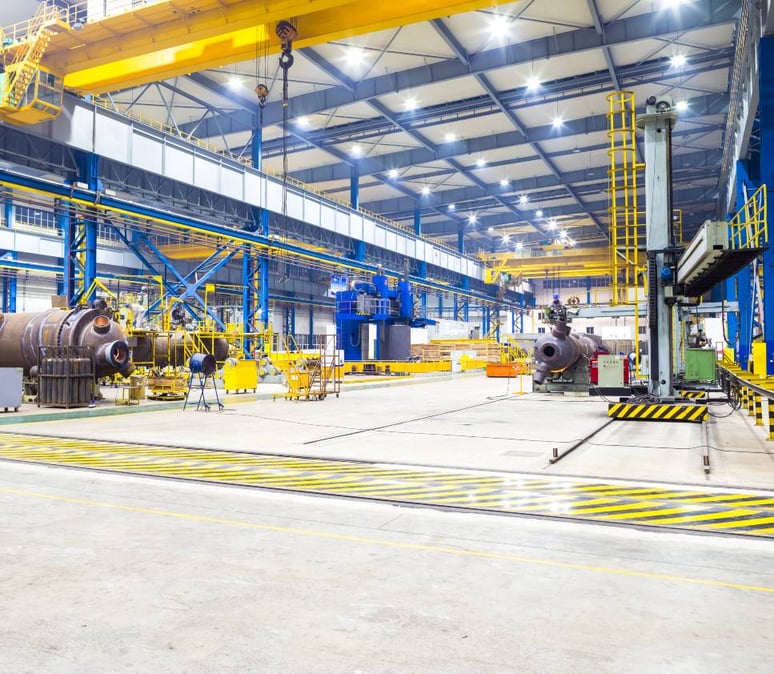
6. Space Utilization
The Space Utilization principle involves maximizing the use of available space for handling and storage activities. Warehouse space is often at a premium - even in terms of overhead space - and the same is true in manufacturing environments. When considering space utilization, ask yourself:
- Can the available space be better utilized for storage and movement?
- How can the available space be maximized for material handling?
7. System
The Systems principle involves using a coordinated system of processes, equipment, and people to improve material flow, improve operational efficiency and reduce waste. When considering the system principle, ask yourself:
- Are there a coordinated system of processes, equipment, and people?
- Can the system be improved to reduce waste and improve efficiency?
A coordinated system is essential to ensure material handling processes, and the wider operation, runs smoothly.
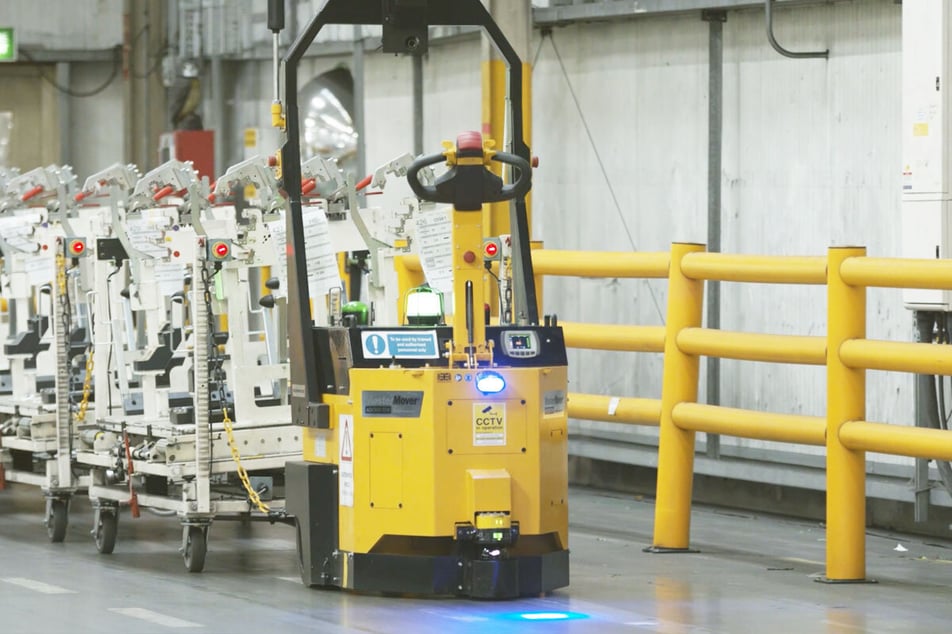
8. Automation
The Automation principle involves using technology to automate material movement for improved efficiency and safety. When considering automation in material handling systems, ask yourself:
- Can technology be used to automate material handling processes?
- How can automation improve efficiency and safety?
Ultimately if a material handling task is being repeated often, and especially where it involves regular travel times, AGV solutions could be the answer.
9. Environment
This involves considering the impact of material handling processes and material handling systems on the environment and taking steps to reduce waste and improve sustainability. When considering the environment, ask yourself:
- What is the impact of a material handling process on the environment?
- How can material handling systems be made more sustainable?
Utilizing battery-powered material handling equipment is often a good place to start, with simple charging, zero emissions and a quieter running noise level.
10. Life Cycle Cost
The Life Cycle Cost principle involves considering the total cost of material handling processes, including material handling equipment and time to run them. When considering the entire life cycle cost of material movement processes, ask yourself:
- What is the total cost of material handling processes over the life of the equipment and processes?
- How can cost be reduced through better equipment and process selection?
Sacrificing productivity by not investing in the right equipment and processes will only have a negative impact ultimately.
Using the Principles of Material Handling to Drive Operational Efficiency & Safety
Following these ten principles of material handling can have several benefits for businesses, helping them to:
Improve operational efficiency
Maximize workplace safety
Reduce costs and waste
Improve sustainability
The ultimate guide to material handling
Material handling equipment
Looking to understand material handling in a little more detail?
We’ve compiled some helpful resources to get you started.
-
Advanced Material Handling Solutions
-
Material handling in manufacturing
-
Forklift Trucks vs. Electric Tuggers
-
Shunters vs. Electric Tuggers
-
Tow Tractors vs. Electric Tuggers
-
Overhead Cranes vs. Electric Tuggers
-
AGVs vs traditional MHE
-
A Forklift-free Future
-
What is Intralogistics?
-
Diesel Forklift Alternatives
-
Benefits of cart tuggers
-
Industrial electric carts
Choosing the Right Material Handling Equipment
By asking yourself the right questions for each principle and implementing the necessary changes, you can create a material handling process that boosts operational efficiency, is safe, and is sustainable.
Remember, every material handling task is different, so it's important to consider each principle carefully and tailor your approach accordingly.
Flexible Material Handling Solutions
MasterMover electric tugs and tows have been designed with many of the 10 principles of material handling in mind. So, if you are looking for the right equipment to drive efficiency and safety when moving loads on wheels, please get in touch!
We're here to help
If you’re looking to improve safety, reduce the risk of injury and unlock greater operational efficiency through effective material handling equipment, we’re here to help. Speak to our team to discuss your application...