8 Material Handling Challenges for Pharmaceutical Facilities

The manufacture of biopharmaceutical products is a complex process. In addition to the challenges facing most manufacturers, biopharmaceutical companies also have to work within highly controlled cleanroom environments, which are enclosed areas where the concentration of environmental pollutants such as dust, microbes, and particles are controlled and classified accordingly.
In addition to stringent environmental requirements, biopharmaceutical facilities utilize an array of heavy, cumbersome wheeled process equipment within their processes. The movement of this heavy equipment presents a challenge to manufacturers and research facilities alike.
This leaves facilities with the task of exploring solutions that can handle significant weights, cleanroom environments, delicate floors, tight spaces, and high-value loads and materials.
Identifying the most suitable pharmaceutical material handling solution that addresses these challenges and delivers the performance needed can be a long and expensive process. The search can feel overwhelming, but with 25 years of experience in solving these challenges for biopharmaceutical facilities, we can help…
Here, we look at how to overcome 8 common concerns to help you find the perfect solution.
1. Understanding the Weight You Need to Move
The first consideration is the capacity of your load-moving solution in relation to the weight of the intended product, equipment, or material being moved. Simply put, this determines the maximum weight the equipment needs to be able to move.
Whether you are looking to reduce manual handling in the movement of single-use mixers, or you need an efficient solution to speed up the movement of large chromatography columns, understanding the maximum weight to be moved is critical. It’s important when calculating the maximum weight that this includes the equipment itself, any skid systems, and product or media weight.
Understanding the maximum weight you need to move and the environment in which you are operating – whether a cleanroom or otherwise – helps to deepen your understanding of which electric tugger or other load-moving solution may work best for you.
2. Knowing Your Space.
Another essential consideration is the space and obstacles within your cleanroom environment. From doorways to other equipment, room layout can provide challenging operational and time issues, especially for suite changeovers.
Electric tuggers are highly maneuverable with flexible steering that enables easy movement. Operators have complete control of movement which reduces the risk of collisions with walls and other objects in tight spaces.
3. Protecting Your Flooring and Considering Rolling Resistance
Cleanrooms, along with test labs, feature delicate floors that are susceptible to damage from heavy weighted objects being moved or pulled. Flooring is a major consideration when selecting a load-moving solution, and a system that can bare the weight of a load, or that is able to significantly reduce the impact, is a solution worth considering.
Floors in clean room environments are also typically high quality, reducing rolling resistance – a key factor when selecting a load-moving solution. A lower rolling resistance means less push or pull force is required to move a load, in effect increasing the capacity of an electric tugger. Where a surface is poor quality, with higher rolling resistance, more power is needed to achieve movement.
Many MasterMover electric tuggers use an innovative hydraulic weight transfer system that creates traction. Our tuggers use a clever coupling system that interfaces with your equipment to transfer some of the load weight through the industrial polyurethane drive wheel, enabling easy movement of loads right up to 44,000 lbs. (or more when rolling resistance is lower!).
Electric tuggers also feature non-marking, puncture-proof tires, which helps to eliminate the risk of damage to flooring during movement.
4. Working in Sterile Environments
Cleanroom suites are tightly controlled, classified environments designed to prevent contamination in manufacturing. This presents a key concern and challenge for facilities looking to introduce handling equipment like electric tuggers into their environment.
With equipment being moved between different locations and departments within a facility, the requirements for the use of solutions that are IP-rated, 316-grade stainless steel and provide zero-emissions, is essential.
MasterMover’s range of stainless-steel electric tuggers work in some of the most stringent cleanroom environments in the industry and our design means they are compatible with all common cleaning agents. With an easy-to-clean 316-graded stainless steel construction, and a range boasting ingress protection of up to IP55, our electric tuggers are built to the stringent cleaning needs of the industry.
5. Ensuring Smooth Movement of High-Value Loads
Pharmaceutical equipment, from chromatography columns to drums and containers, pressure vessels and buffer containers, typically contain valuable media requiring careful movement and positioning.
The challenge faced by pharmaceutical facilities is to reduce or eliminate these risks with a solution that runs smoothly. With the hydraulic weight transfer system used in our electric tuggers, loads are moved smoothly, controlled with ease, and can be stopped quickly – in a controlled manner – to prevent damage.
The compact nature of our electric tugger systems also means that operators can easily position and maneuver large equipment such as chromatography columns in tight environments. With speed control functionalities and a responsive emergency stop button as standard, you can avoid costly damage and collisions.
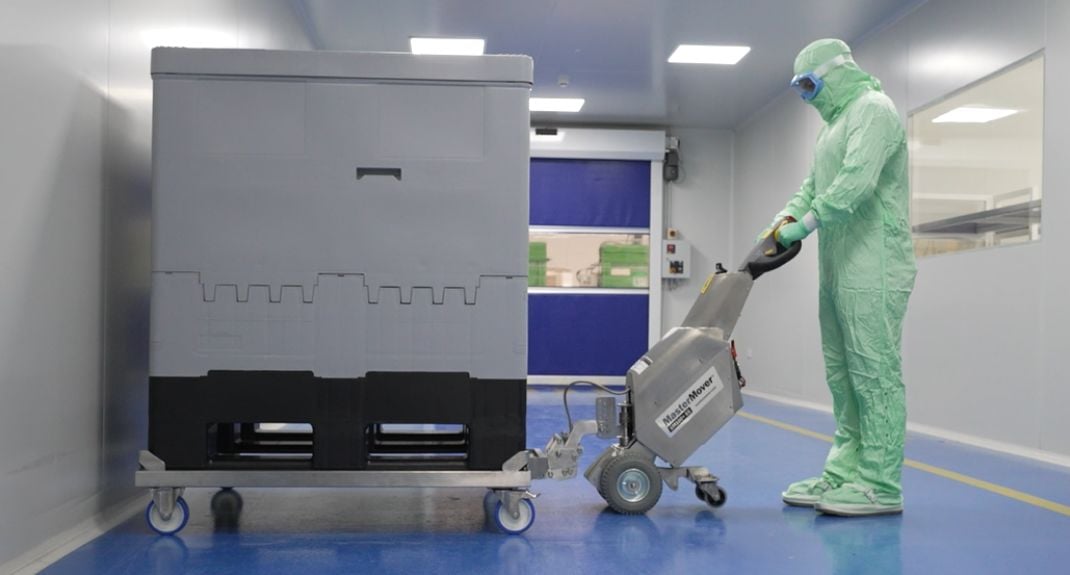
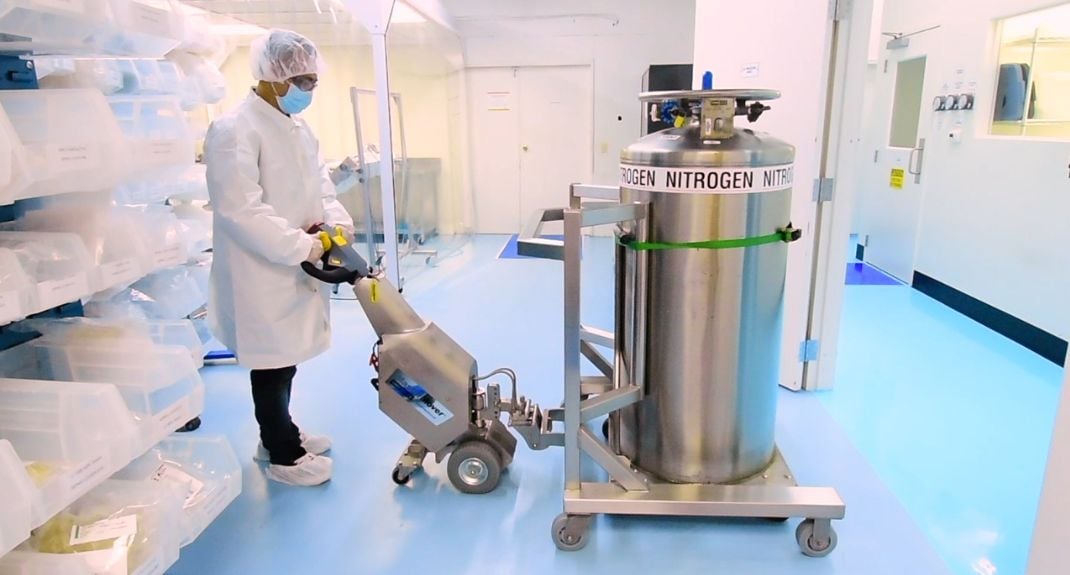
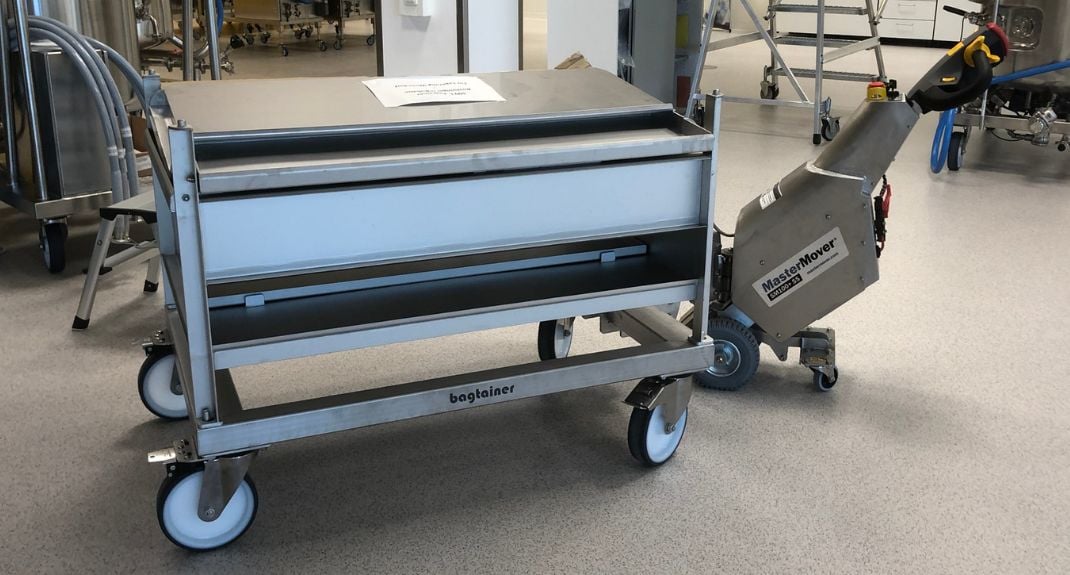
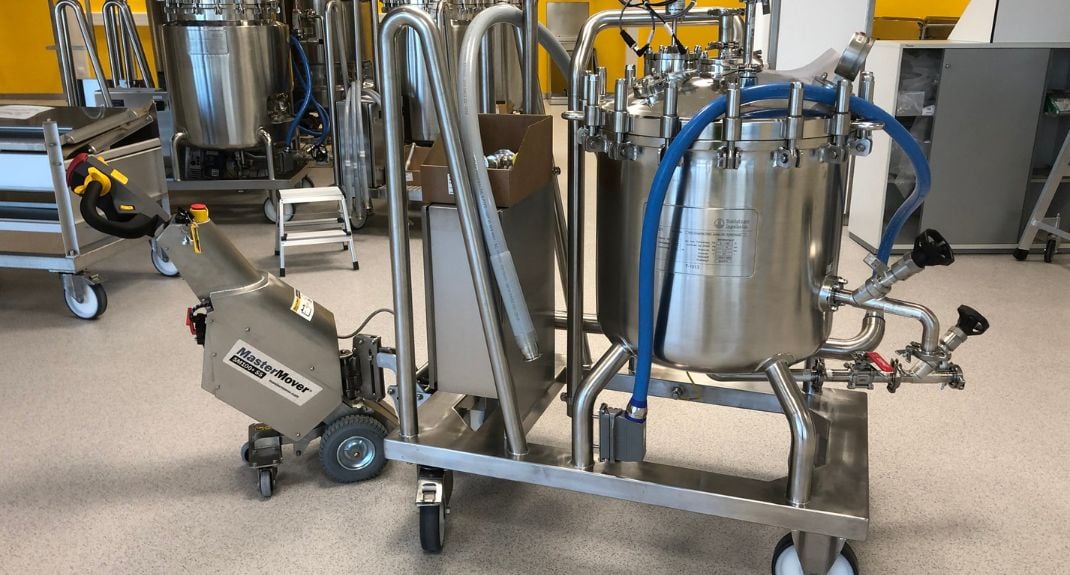
6. Optimize Staff Utilization
With highly educated and trained staff, optimizing your resources and staff productivity is critical. Manual handling is common in the industry, especially when moving tanks and mixers weighing around 2,200 lbs. Aside from the obvious safety issues, the manual movement of wheeled equipment often requires multiple members of staff, taking them away from value-adding activities. With this also comes the added pressure associated with manual handling injuries in staff absences.
Using a solution that complements your existing staff structures, removes the need for physical exertion and requires minimal training that anyone can control can significantly help in maximizing production efficiency.
Electric tuggers are simple to use and require no operator license. They can therefore be used by a range of people as required, and as they eliminate manual handling, a single operator can move even the heaviest loads.
7. Maximize Production and Cleanroom Changeover
One of the main frustrations and additional stresses for pharmaceutical environments is production timing and capacity. Being able to move equipment safely, and change suite configurations quickly, is essential to maintaining an efficient production facility.
From the initial setup, system maneuvering, and changeovers, the movement of process equipment can add extra time to tasks and activities, creating an unnecessary and often complex production schedule.
With an electric tugger, you can make equipment movements a one-person job, helping you maximize suite uptime, create efficient changeovers and increase your flexibility.
8. Knowing your desired ROI
Striking a balance between budget, cost and desired benefits is a challenge present in all industries, but no more so than within the biopharmaceutical sector. As with any equipment, assessing the feasibility of handling equipment involves the upfront investment, installation and any ongoing maintenance costs. An important, but often overlooked aspect to consider when implementing handling equipment is having a strong understanding of your desired return or benefits.
For Health & Safety Managers within pharmaceutical facilities, the core aim may be in reducing or preventing staff injuries and absences through the manual movement of equipment.
For Process Staff, the desired return might be in achieving an increase in suite uptime, by reducing the time taken to complete changeovers.
Whatever your desired benefit or return on investment, it’s important to understand the problem or challenge you wish to solve and weigh this up against the perceived cost of equipment.
Our electric tugger solutions are used by manufacturers to complete an array of tasks within the industry, but the core benefits they deliver remain the same across the globe. They create a safer working environment for staff by reducing manual handling injuries and facilitating quicker suite changeovers to increase production efficiency.
A Solution That Meets Your Needs
After reviewing the challenges of material handling in the pharmaceutical industry and the benefits of stainless steel electric tuggers, it’s clear that they are a valuable asset within the manufacturing process.
Large-scale manufacturing is a process that relies on dependable methods and produces a high volume of finished products. The quality of the end product is often reliant not only on the quality of the raw materials but also on the accuracy of the intermediate processes.
In the pharmaceutical industry, this is even more true. It’s vital all stock, equipment and finished goods are handled with care. Our electric tuggers help manufacturers achieve pinpoint accuracy and positioning, enabling them to reduce the risk of damage to high-value equipment.
Manufacturing output can also be affected by changes in demand, and an electric tugger can help reduce the impact of these changes on production layouts by being able to quickly adapt to differing requirements. The need for agility is critical and electric tuggers enable the swift reconfiguration of production layouts to help pivot operations in line with demand.
If you’re looking for a material handling solution that can improve efficiency and safety in your facility, MasterMover has a wide range of sector-specialist solutions utilizing the latest tools and technology.
Get in touch today to see how we can help you optimize your suite efficiency with our electric tuggers.