Forklift-free Future
Material handling equipment
With many of the world’s leading manufacturers investing in forklift operations, and an array of solutions are available on the market to help.
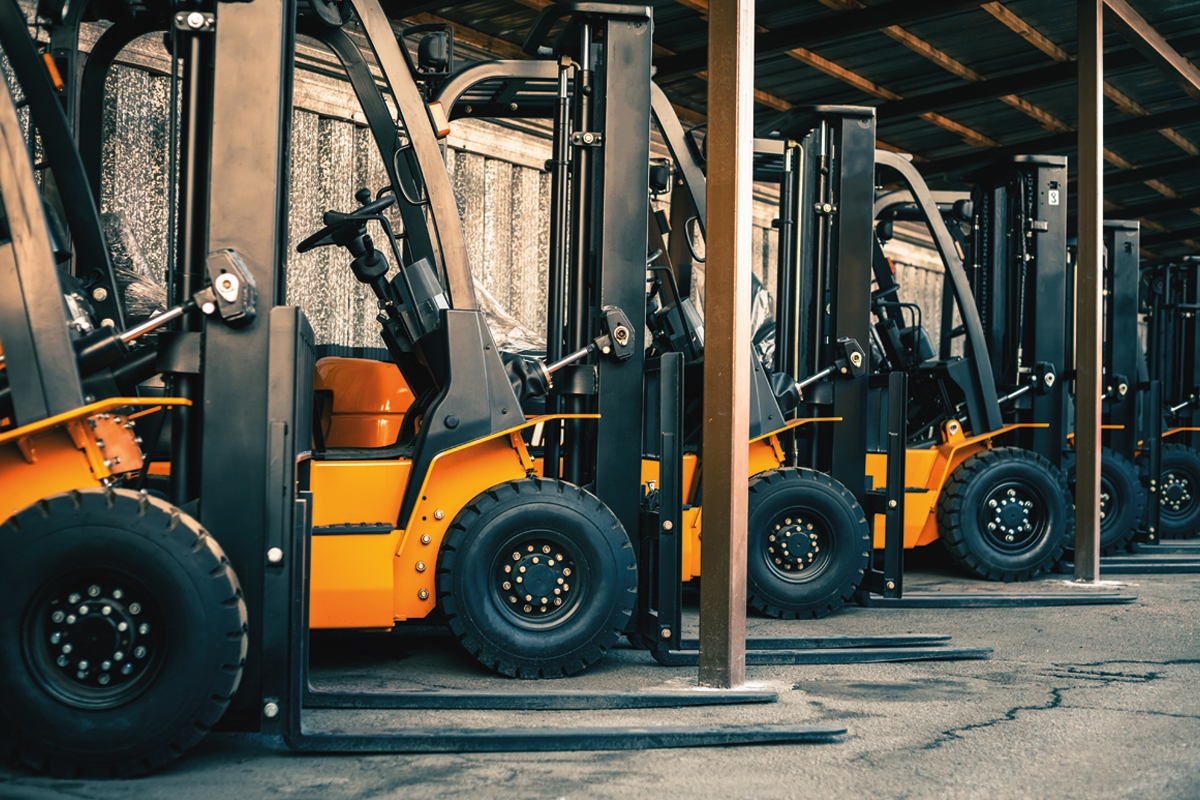
The future is forklift free, but what is it?
Many of the world’s largest manufacturers and Fortune 500 companies continue to make their operations fork-free.
Here’s why you should too…
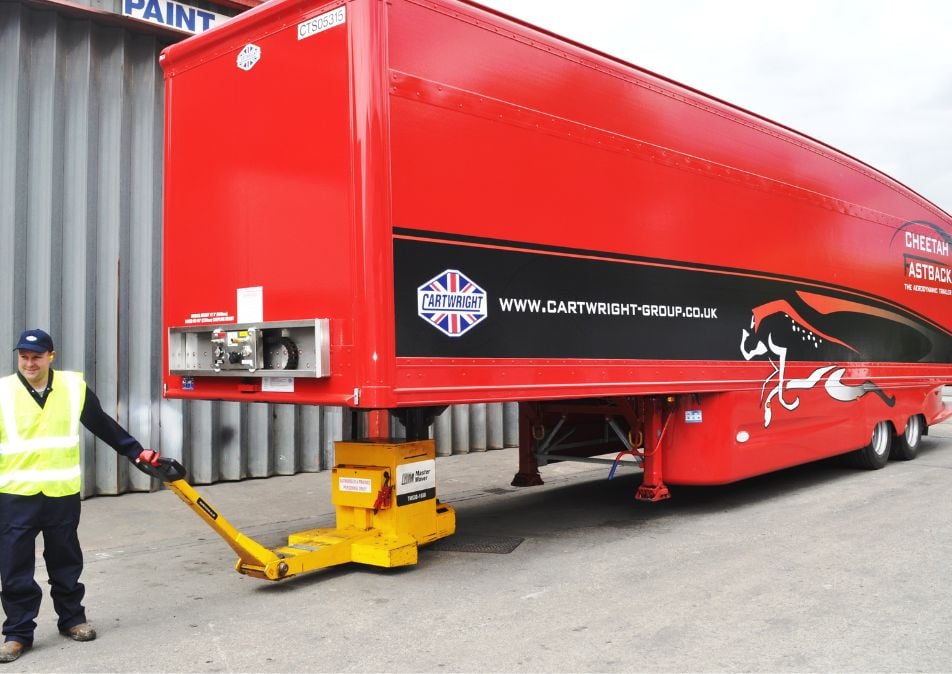
So, what’s forklift-free?
Forklift-free is a term used to define production operations that no longer use forklifts or lift trucks in their processes.
There are many reasons manufacturers are removing forklifts from their production areas, but the main reason for most EHS Managers is simple – safety.
Forklifts are large, powerful and useful pieces of equipment, designed to LIFT. They require trained, licensed operators to drive, but operating forklift trucks in busy, congested shop floors poses a big safety risk. Often visibility is difficult when moving loads. Couple this with noisy and populated work areas and even a horn or movement sensor isn’t going to remove the risk of collisions.
While forklift manufacturers undoubtedly continue to add safety systems and features to their trucks, forklifts still pose a real safety issue for many manufacturers.
The risk of forklift trucks colliding with pedestrians in busy areas is a big issue in manufacturing and one that many companies are tackling by simply removing forklifts from their shop floors or creating fork-free zones. McCue reports that 36% of forklift-related deaths are pedestrians – showing the extent of the risk that many manufacturers are tackling through fork-free zones (McCue, 2021).
Forklift truck incidents statistics
-
43% of forklift incidents involve pedestrians
Data source: NFSD, 2020 -
On average 95 people are seriously injured in forklift accidents every day and 1 person is killed in a forklift accident every 4 days in the United States
Data source: McCue, 2021
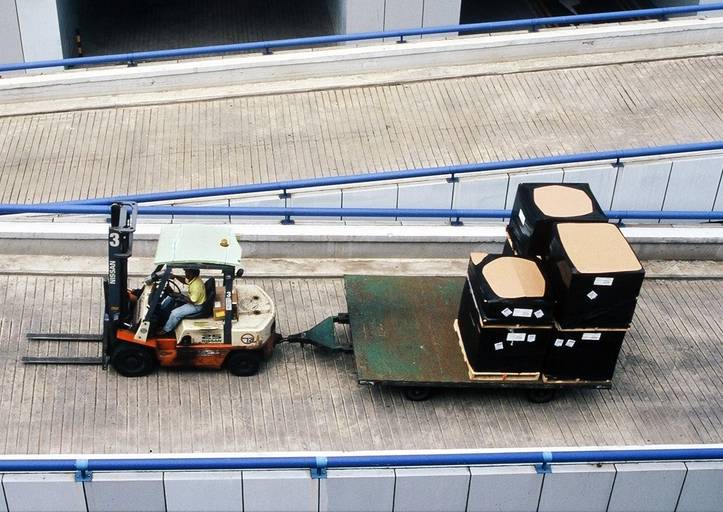
The cost of forklift misuse – Towing with a forklift is a big NO!
As the name suggests, a forklift is designed to lift, not tow. However, as with many useful tools and pieces of industrial equipment – the forklift tends to be misused or have its’ abilities stretched.
“But most forklifts come with a towing point at the rear!”
This is where people get confused or, try to cut corners and costs. The towing point on a forklift ISN’T to tow a trailer, or a train of carts or attempt a 36-point reversing maneuver of a flatbed in your warehouse.
It IS to recover the forklift truck in the event of a breakdown.
Most manufacturers and reputable forklift providers advise against using it as a towing unit because units aren’t designed to be used to tow. There are several reasons for this, but the main one is it creates a high tipping risk. This is especially true for models with rear-wheel drive, where front-wheel braking systems can make the units unstable when towing.
You’ve likely heard the horror stories of forklift tipping – the results of which can be fatal.
There’s an array of material handling equipment on the market from electric tuggers, tow tractors and ride-on-tows that are specifically designed for this application, which is another reason many manufacturers are moving to fork-free operations.

No forklifts…now what?
In removing forklift trucks from the shop floor, many manufacturers are adopting systems focused on modularity and mobility. This ranges from simple cart systems, all the way through to fully automated carts and autonomous vehicles. There are an array of solutions on the market available for manufacturers of all shapes and sizes and of course varying budgets.
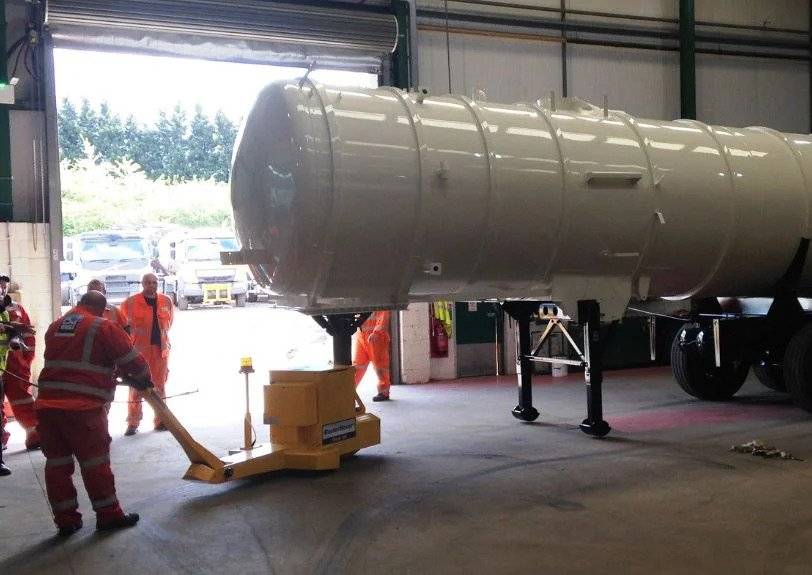
Don’t replace one risk with another…
The concept of forklift-free presents an array of benefits, but it is critical that operational factors are considered before taking the leap.
For example, removing forklifts from the shop floor and introducing wheeled carts will provide flexibility – but then expecting staff to manually push or maneuver these carts cancels out any potential benefits of forklift-free. By doing so, you have ultimately replaced one risk with another. That’s why it’s important to fully assess your processes, existing systems and highlight any potential new equipment needs.
For many manufacturers, when implementing forklift-free areas, carts are coupled with appropriate handling systems such as electric tuggers or tows. This way, you benefit from the shop floor safety improvements of reduced forklift traffic, while also introducing an appropriate solution to mobilize your new systems safely.
3 benefits of forklift-free and electric tuggers
Moving towards forklift-free operations presents opportunities to reduce lifting requirements and mobilize goods and sub-assemblies through wheeled tugger and cart systems. This enables you to improve shop floor safety, improve your ability to pivot operations and quickly change production layouts.
-
1. Reduces hazards and risk of injuries
-
2. Improves your shop floor flexibility
-
3. Reduces your transport times and downtime
1. Reduces hazards and risk of injuries
Simple, but invaluable – improving safety.
That’s one of the main reasons many manufacturers are switching up their processes and removing forklifts from their shop floor. Swapping your handling systems to electric tuggers and cart systems means you benefit from:
- Reduced risk of collisions with pedestrians
- Improved operator visibility (especially true with remote control tugs)
- Loads stay safely on the ground – meaning reduced risk of falling loads
- Mitigates any potential need for manual handling through mechanized movements
2. Improves your shop floor flexibility
Something we’ve all seen an increased need to be over the last few years is flexibility.
Fixed processes and cumbersome equipment reduce your ability to pivot and change your plant configurations – which, in turbulent times, matters.
Replacing forklift operations with tugger and cart systems improves your plant's flexibility, modularity, and mobility – meaning equipment can be easily moved as required.
3. Reduces your transport times and downtime
It doesn’t matter if your plant brands its operational thought-processes as lean or any of the other schools of thought, the main aim of the game for most is to reduce waste in your operations.
Wasted material or inventory, waste manpower, defects, and over-processing – are all types of waste covered under lean thinking. Others include ‘motion’, ‘waiting’ and ‘transport’, all of which a fork-free operation will help you address. Moving to fork-free operations will enable you to reduce excess motion, particularly in the form of lifting. In addition, there will be no more waiting around (downtime!) for a licensed forklift truck driver, with no operator license required for electric tuggers, your operations can keep on moving, allowing you to reduce downtime and wasted time.
The future is forklift-free, are you ready?
With many of the world’s leading manufacturers investing in forklift-free operations, and an array of solutions on the market to help you reap the benefits of mobile and modular operations, now is the perfect time for you to make the switch.
At MasterMover we provide electric tuggers and custom cart systems as well as industry-leading advice to help you mobilize your operations the safe way.
The ultimate guide to electric tuggers
Electric tugger essentials
Looking to understand electric tuggers in a little more detail?
We’ve compiled some helpful resources to get you started, covering everything from how they work, different types of batteries, to getting the right connection point and more…