Top 10 Benefits of AGVs
AGV Systems
When deployed correctly, AGV electric tuggers and other material handling equipment offer better ROI, increased safety, and a more efficient operation.
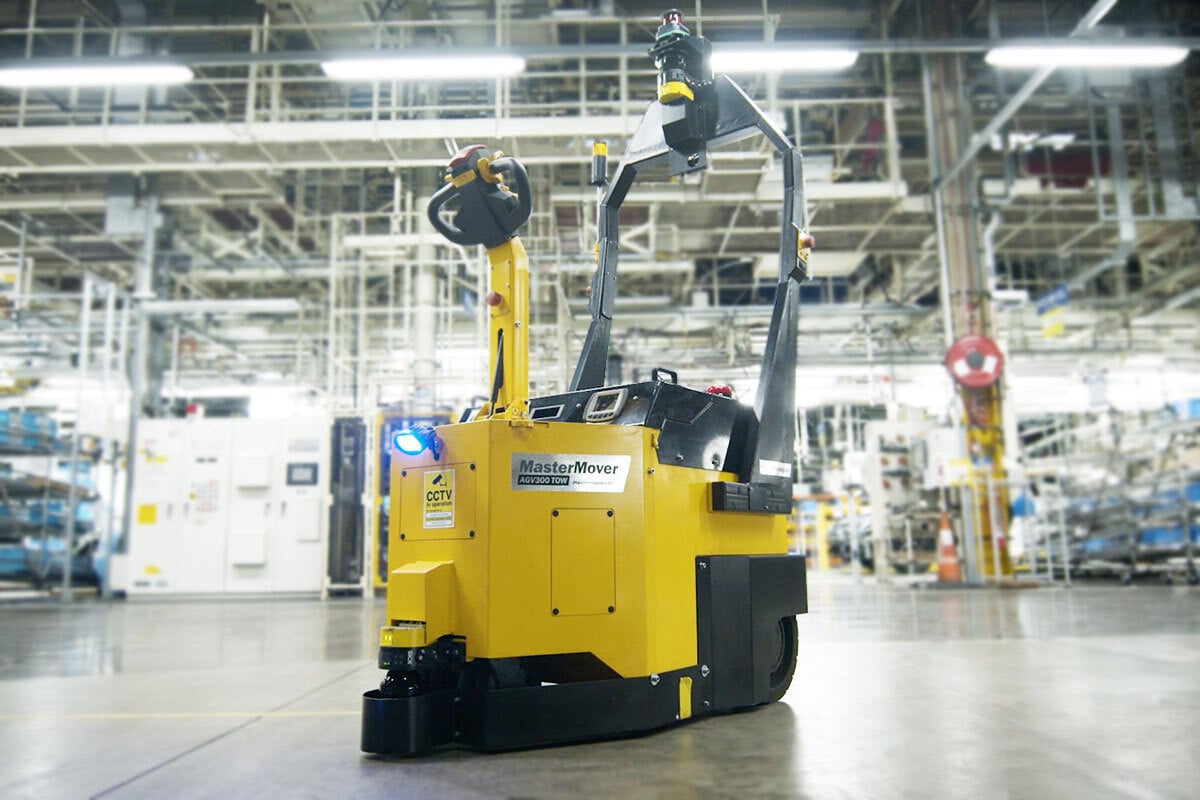
An introduction to AGVs
Automated Guided Vehicle (AGV) electric tuggers are becoming increasingly popular in Industrial Manufacturing sectors. And it’s not difficult to see why, as they’re designed to autonomously move through your environment without the need for an operator.
There is often a hesitancy to adopt AGV solutions despite the many benefits. Concerns center around perceived cost, risk in terms of safety, and fear of change. Yet when deployed correctly, AGV electric tugs and other material handling equipment offer better ROI, increased safety, and a more efficient operation.
MasterMover works with best-in-class safety and navigation technology providers and this, coupled with 25 years of engineering experience, delivers a world-leading AGV solution that maximizes safety and operational efficiency.
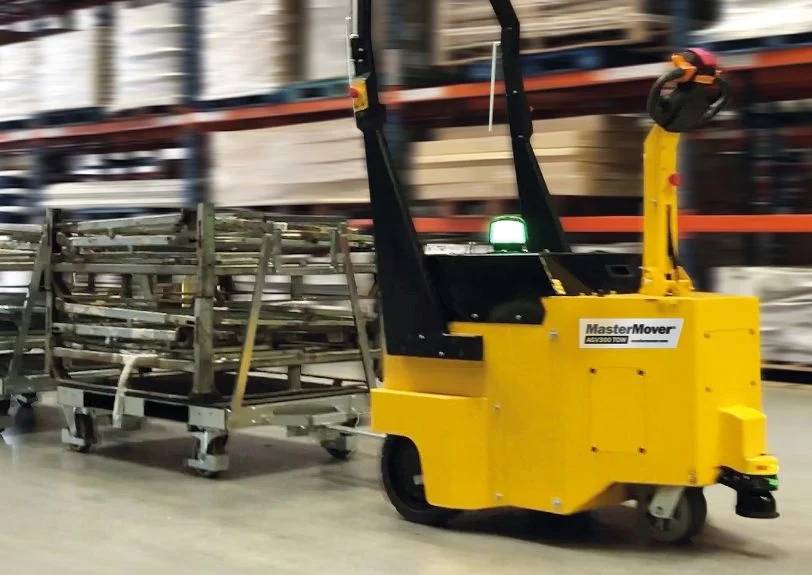
What is an AGV?
AGV stands for Automated Guided Vehicle. It is a mobile unit that utilizes floor markings or onboard navigation and sensors to travel between locations. Typically, they are used in industrial manufacturing and logistics settings.
A wide range of AGV solutions exist focused on carrying out high-volume tasks while moving products, equipment, and materials of lower weights. MasterMover, however, offers AGV solutions capable of moving loads up to 44,000 lbs. and beyond.
For example, our TOW300 is used in automotive manufacturing by a well-known car maker. The AGV is used to move parts to the production line and empty units away from it, offering the capability to move up to 6,600 lbs., using navigation and sensor technology.
The AGV TOW300 gives 10 hours of operation between charges and carries out tasks more efficiently than could be achieved through a more human-involved process.
10 Benefits to utilizing AGV electric tugs
-
1. Better utilization of people
Eliminate or reduce the need for your staff to spend time moving materials. AGV solutions make movement of equipment and materials more efficient and allow your people to spend more time doing tasks of greater value-add.
-
2. Allows precise, accurate movement
AGV solutions are ideal when working in tight spaces, or when moving a load through areas with minimal clearance.
-
3. Repeatability
AGV’s deliver a repeated movement and repeated precision, which matters in a busy manufacturing environment.
-
4. Eliminate human error
AGV material handling equipment eliminates this risk by taking control away from a human operator. Safety sensors ensure a programmed response to any detected risk, stopping movement until a hazard has been cleared or moved away.
-
5. Maximize safety
AGV electric tuggers can be programmed to take action such as reducing speed in certain locations when visibility is reduced, or when the surface becomes wet and traction is impacted.
-
6. Better efficiency
An AGV will travel to its destination at a set speed, faster than if the movement was conducted manually, or by pedestrian-operated equipment by a person who could be delayed or distracted.
-
7. Cost & redundancy vs fixed automation systems
AGV electric tuggers are more cost-effective than fixed automation systems.
They are more flexible in terms of being able to carry out a wider range of tasks. Additionally, they are more redundant as they can easily be swapped out to minimize any disruption caused through faults.
-
8. Maximizing investment ROI
MasterMover AGV electric tuggers can be switched to manual operation, so if the need arises, the machine can be taken off its typical tasks and utilized to move any wheeled load within its weight capability.
-
9. 24/7 operation
AGV electric tuggers that are battery-based offer 24/7 operation. The only consideration is battery charging and replacement (if using multiple batteries).
MasterMover electric tuggers can be supplied with spare batteries, which can be stored and charged whilst the machine is in operation. This battery can then be swapped out in between tasks for minimal downtime.
-
10. Consistent & reliable
Not only are AGV’s consistent in their function, but they also have relatively consistent costs compared to manual labor and are affordable to maintain. MasterMover electric tugs are made to the highest standards, so are reliable solutions that deliver day after day.
Utilizing Technology to Go Beyond Pedestrian-Operated
AGV’s move using a combination of software, scanners and sensors. Most are set to follow a defined path that can be specified by the operator. Others use sensors and scanning systems that allow them to detect the environment around them to navigate around obstacles.
Beyond pedestrian-operated electric tugs, there are 6 “levels” of technology available from MasterMover, building up to a full AGV solution:
Remote Control – Forwards & Backwards
For simple applications or loads on rails, this AGV option involves wireless control to move between two points.
Remote Control – Multi-Directional
Full remote-control capacity enables machines to be driven with the use of a wireless transmitter.
Remote Control – MultiLink
MasterMover MultiLink technology means two or more machines can be wirelessly synced together for fleets that can be managed by a single operator.
Remote Control – Line Follow
Machines use sensors with line reading technology to read painted or taped lines on the ground. This ensures a set path is followed. Operators can control the speed of the machine. A great solution for moving through a tight space where repetition of movement is essential.
AGV - Line follow
As above, but no operator is required. Barcodes can be placed on the ground and can be scanned by the machines for additional controls to be programmed, such as slowing down through a specific area.
AGV – Natural Navigation
Natural Navigation allows machines to navigate autonomously by identifying and mapping the surrounding area.
An AGV that fits your application
Regardless of your current phase, we understand that switching to an AGV system is an investment, even if it is one that will inevitably deliver increased ROI, efficiency and safety. Our skilled and experienced team is here to guide you with our tried and tested approach.
Our 5-step process:
-
1. The right machine for you
Firstly, we put time into understanding your application.
-
2. The right navigation for your site
We’ll explore which navigation system works best.
-
3. The right dispatch commands
Next, our team will look at how the AGV gets its instructions to move or ‘pulse’ to the next location.
-
4. Integration with your systems
Then, we look at where other system integrations are needed.
-
5. Optimize your safety systems
Depending on the environment and application, identifying the right safety systems is key.
Case Study – See an AGV electric tugger in action
If you’d like to learn more about MasterMover AGV electric tugger solutions and discuss how they could benefit your operation, we’d love to hear from you.
As we have seen with many customers, AGV electric tuggers deliver outstanding operational performance, helping manufacturing and logistics companies to drive efficiency and maximize safety.
The ultimate guide to AGV electric tuggers
Automated Guided Vehicles (AGV)
Looking to understand AGV systems in a little more detail?
We’ve compiled some helpful resources to get you started, covering everything you need to know.