Total Control for Hubbard Products
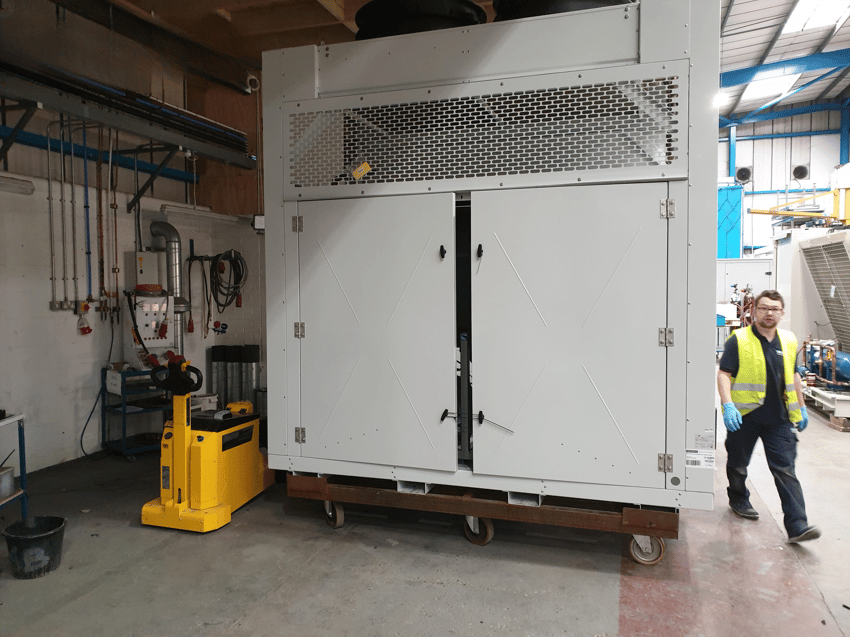
For Hubbard Products, one of the UK's leading manufacturers of commercial cooling equipment, the MasterMover MT600+ was the only solution for them when it came to safely transporting heavy components through a busy factory.
Moving 6,000kg of steel with a forklift truck is no easy feat. Difficult balance and a limited turning circle mean that production processes can often take longer than necessary, a challenge that Hubbard Products' Ipswich site had been struggling to overcome.
It has given us far greater flexibility. Now we’ve got it, we can’t imagine life without it.
Derek ChapmanDesign Office Supervisor, Hubbard Products
The challenge
Forklifts, while commonly used in industrial settings, have inherent limitations that can make them less than ideal for specific tasks:
- Safety risks: The weight and size of the loads requires precise balance. Any slight misjudgment could lead to instability, risking damage to components or injuries to employees
- Limited manoeuvrability: Forklift trucks have a restricted turning radius, which can make navigating tight spaces within a busy factory floor challenging.
- Operational inefficiency: Forklifts require a licensed operator and often need a second person to act as a spotter, particularly when moving large or awkward loads. This dependency on trained personnel creates bottlenecks when licensed operators aren't available.
Derek Chapman, Design Office Supervisor at Hubbard Products, summarised the issue: “Watching six tonnes of steel being moved by forklift truck made me nervous.” Recognising the inefficiencies and risks, Derek and his team sought a solution that could streamline their processes whilst also improving safety.
The solution
Hubbard Products wanted a better solution for moving build dollies containing heavy parts for the manufacture of industrial refrigeration systems. So, after speaking to the manufacturing and assembly specialists here at MasterMover, a trial was set-up using the MT600+ machine which offers the following benefits:
- Enhanced safety: Unlike forklifts, the MT600+ enables the operator to remain at ground level, offering all-round visibility and reducing the risk of accidents. It also features a self-adjusting castor guard to prevent foot entrapment during operation.
- Improved manoeuvrability: The compact and powerful design of the MT600+ allows precise control in tight spaces, making it far better suited for factory environments than a forklift with a limited turning circle.
- Operational flexibility: With simple training provided by MasterMover, any staff member can operate the MT600+, eliminating the reliance on licensed forklift operators and the need for additional guiding personnel.
As Derek Chapman noted: “Our components are precisely balanced and, when these were being moved with a forklift truck with a limited turning circle, it was proving difficult. Now we can move the loads safely and easily while keeping components at ground level.
"The other advantage is that, after training from the MasterMover team, anyone here can use the MT600+. We no longer have to wait for a licensed forklift truck operator to become available and there is no need to have another person guiding them while they’re moving loads."
A permanent fixture
With the MasterTug now a permanent and integral part of operations at Hubbard Products, Chapman confirms that: "It has given us far greater flexibility. Now we've got it, we can't imagine life without it."
Hubbard Products’ experience highlights the transformative potential of electric tugs like the MT600+ for manufacturers handling heavy materials. By replacing traditional forklifts with innovative solutions, businesses can achieve safer, more efficient operations while empowering their teams with greater flexibility.
Our comprehensive range of electric tugs offers solutions for industries worldwide, with the capability to move loads from 50 kg to 360,000 kg. Whatever the challenge is, MasterMover can help reduce material handling pressures and create a safer workplace.