The Ultimate Tugger AGV Guide from Automation Expert, James Jones
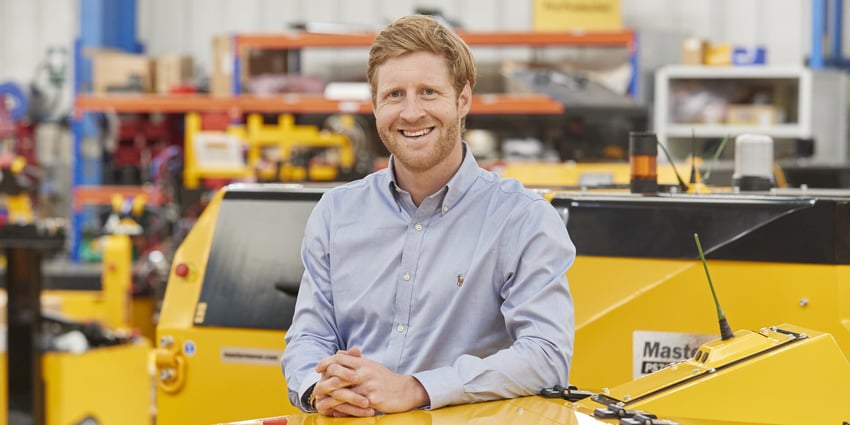
Tugger AGVs (Automated Guided Vehicles) are becoming an essential tool for businesses looking to enhance efficiency and streamline operations. By automating repetitive towing tasks, these vehicles allow companies to optimise workflows, reallocate labour, and achieve significant cost savings.
James Jones, Director at MasterMover and our in-house automation expert, shares his expertise on the key considerations for businesses looking to purchase tugger AGVs.
AGV applications and benefits
Towing or tugger AGVs are widely used to automate towing processes, making them particularly popular in the automotive and logistics industries. However, their applications extend far beyond these sectors. These AGVs are designed to pull trolleys or carts in a train formation, making them ideal for environments where loads need to be moved over long distances with multiple drop-off and pick-up points.
Manufacturing and heavy plant applications
In manufacturing for instance, tugger AGVs handle repetitive tasks such as delivering components, parts, and equipment to production lines. In the automotive industry, they enable seamless sideline deliveries, supporting just-in-time production systems. Heavy plant assembly lines also benefit, as these vehicles can:
- Precisely transfer work-in-progress and sub-assemblies through various production stages.
- Reduce the need for manual intervention, ensuring smoother processes.
For example, we recently worked with Toyota to roll out towing AGVs for exactly this, to improve their operational efficiency and labour utilisation in the movement of resin backdoors at their factory in Derbyshire, UK. Previously, the driving process was completed using a ride-on tow tractor and a licensed driver. This meant that each shift needed dedicated resources for the process. Identifying this as a non-value-adding activity and an area of waste, Toyota decided to work with us to automate this process and maximise efficiency.
Logistics applications
For logistics, tugger AGVs offer a scalable and efficient alternative to traditional forklift systems. One notable example involves a 3PL provider that used tugger AGVs to move roll cages within a logistics depot. Previously, forklift trucks were used to transport these cages across the site. However, forklifts could only move a limited number of cages at a time and often operated in congested areas. By implementing tugger AGVs, the company achieved:
- A fivefold increase in the number of cages transported in a single trip.
- Improved operational efficiency by automating the movement of stock.
- A reduction in the need for operators to transfer stock manually across the site.
Businesses are increasingly turning to tugger AGVs to address inefficiencies in manual towing operations. Manual vehicles require dedicated operators for tasks that are often low-value yet essential. By automating these processes, companies can free up their workforce to focus on skilled and value-adding activities, resulting in significant productivity gains.
Tugger AGVs are built to handle a diverse range of applications and loads. Our MasterTow AGVs, for example, support loads up to 20,000 kg, with other models capable of towing up to 70,000 kg. This flexibility allows them to cater to industries with varying needs, from automotive trolley trains weighing around 2,000 kg to aerospace and heavy plant applications where loads exceed 10,000 kg.
Load connection and navigation
The way tugger AGVs connect to their loads depends on the specific application. In our 25+ years of designing pedestrian and remote-controlled electric tugs and tows, we’ve found this to be very much customer driven. Simple systems use manual connections, such as towing pins or ball hitches, while advanced operations employ auto-coupling mechanisms. Auto-coupling systems allow AGVs to autonomously hitch and unhitch trolleys without operator intervention, streamlining processes further.
Navigation technologies also vary. Many businesses prefer natural feature navigation, which uses existing environmental landmarks for guidance. This system is highly flexible, requires no physical infrastructure, and is easy to adapt. Alternatively, line-following navigation, which relies on a physical path installed on the floor, offers a more budget-friendly option but requires regular maintenance of the path.
Safety features, hybrid functionality, and outdoor capabilities
Safety is a critical consideration, especially for towing AGVs handling large or complex loads. Integrated safety scanners, adaptive safety fields, and emergency stop systems ensure safe operation even in congested areas. For example, in towing applications where multiple daughter carts follow the AGV, careful evaluation of the route and trolley design is essential to maintain safety and stability.
Hybrid functionality, which allows AGVs to switch between automated and manual modes, is another important feature. This capability ensures operations remain fluid even if the AGV’s path is blocked or if maintenance is required.
To ensure that the towing AGVs can safely work alongside other traffic, a fleet management system will be installed to allow the AGV to communicate and interact with existing automated vehicles and infrastructure such as shutter doors and traffic light systems.
Tugger AGVs can also operate outdoors, navigating slopes, rough terrain, and varying weather conditions. For example, we recently implemented an AGV system for an automotive manufacturer, where the vehicle navigated from an indoor facility through a busy distribution yard to an outdoor warehouse, seamlessly handling the transition between environments.
Integrating AGVs on site
Integrating towing AGVs into existing workflows requires careful planning to ensure seamless operation. When replacing manual towing systems, it’s crucial to account for factors such as load stability, route complexity, and site conditions.
Best practices for integration often involve a phased approach. Instead of rolling out a fully autonomous system from the outset, businesses are encouraged to start with simpler applications. For instance, an automated transfer system between a trolley train and production equipment can be implemented first, with the AGV added later. This step-by-step strategy allows for process refinement and ensures the technology is well-suited to the specific application.
We prioritise close collaboration with customers during this phase, taking the time to truly understand their current needs and future goals. This tailored approach ensures that the chosen solution delivers maximum value and solves client challenges effectively.
Maintenance and ongoing support
Well-designed and correctly specified tugger AGVs will outperform manually driven vehicles and require minimal maintenance but regular checks are essential to ensure optimal performance. Weekly maintenance tasks include cleaning scanner lenses and inspecting the AGV for debris. High-wear components, such as tires and drive wheels, should be checked quarterly.
Telematics and data capture systems can enhance maintenance routines by providing real-time insights into motor temperature, battery performance, and other critical metrics. This enables preventative maintenance and helps identify potential issues before they escalate.
We also provide comprehensive technical support and training to ensure the long-term success of AGV systems. From installation to ongoing remote and on-site support for the lifetime of the product, we pride ourselves on being the go-to AGV partner of choice.
Investing in tugger AGVs
Investing in a towing AGV system requires careful consideration of factors such as safety, reliability, and vehicle design. Safety features like emergency stop systems and adaptive speed settings are non-negotiable, ensuring AGVs can operate securely in diverse environments. Proven vehicle designs are equally important, offering durability, superior braking capabilities, and consistent performance.
The return on investment (ROI) for tugger AGVs is impressive, particularly for multi-shift operations. For example, double-shift scenarios can achieve a 200% ROI over three years, while triple shifts see ROI figures as high as 649% over five years. These returns are driven by reduced labour costs, increased efficiency, and the ability to reallocate employees to more productive tasks versus traditional single operator and vehicle setups.
Tugger AGVs are reshaping the way businesses manage their towing processes, offering unparalleled benefits in efficiency, scalability, and cost-effectiveness. Whether you’re in manufacturing, logistics, or any industry with repetitive towing tasks, these systems can transform your operations.
By working with industry experts with extensive experience in award-winning designs, safety features, and phased integration, companies can ensure a smooth transition to automation to truly maximise their ROI. Complete the form below to discover how our towing AGVs can support your business goals.