An Alternative to Overhead Cranes
Material Handling Equipment
When it comes to material handling in factories, the movement of heavy loads, such as work in progress, tooling, components, and sub-assemblies, presents a significant challenge.
The default for many businesses is to use overhead cranes to move large parts through the factory. As many businesses look to optimise efficiency, a leaner, more flexible solution is emerging – electric tugs.
Thank you for submitting your consultation request.
A member of the team will be in touch shortly.
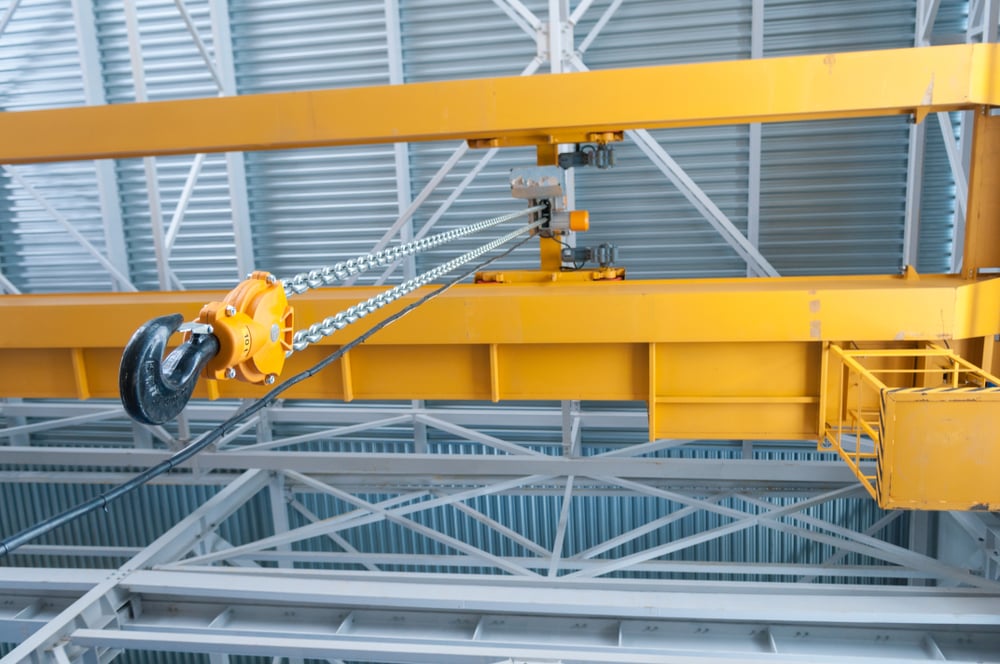
Electric Tugs vs Overhead Cranes
You’d be forgiven for questioning why fixed overhead crane systems and electric tugs are often pitted against each other when assessing material handling solutions.
Both systems work very differently – but ultimately achieve the same core objective of moving a heavy load from A to B.
Both systems offer unique benefits that manufacturers must carefully consider before making a decision. In this blog, we’ll explore the pros and cons of electric tugs and overhead cranes in factories, assessing both solutions against efficiency, flexibility and cost.
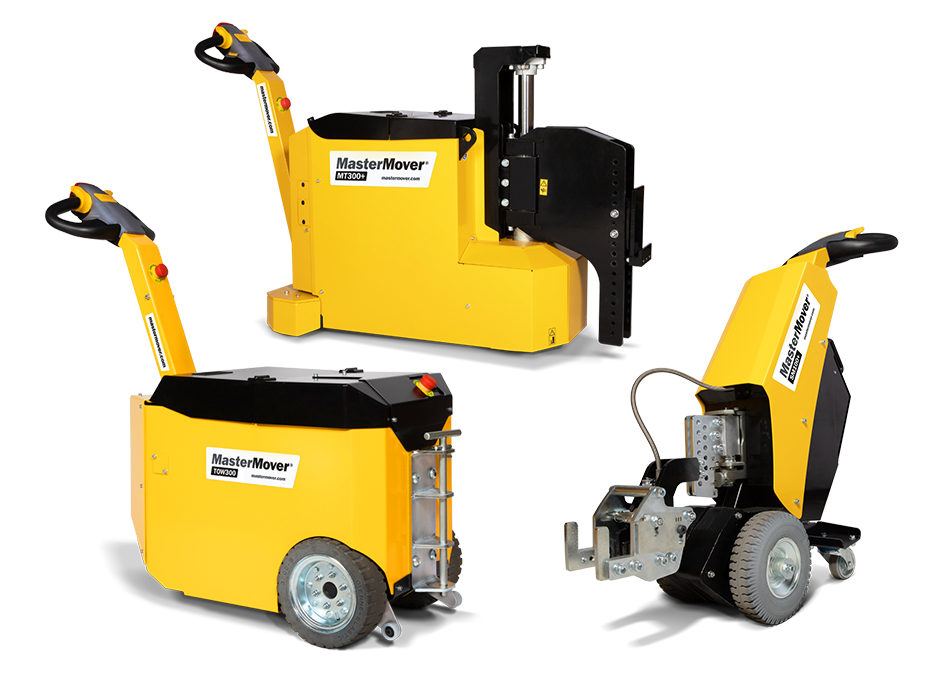
Different Types of Electric Tugs
Electric tugs, also known as electric tow tugs or battery-powered tugs, are versatile and efficient solutions for moving heavy-wheeled loads. These compact yet powerful machines are designed to navigate tight spaces, making them ideal for manoeuvring materials in congested factories. With heavy weight capacities, electric tugs can be used to move loads weighing up to 70,000kg and beyond.
Offering a more mobile, flexible, and safer alternative to forklift trucks, overhead cranes or manual handling, electric tugs are used across industrial manufacturing industries to improve efficiency and workplace safety.
Electric tugs are available with various control options including pedestrian operated, remote control and even as autonomous Automated Guided Vehicles (AGVs).
Different Types of Crane Systems
Cranes are heavy-duty solutions that lift large and heavy loads, typically within factory environments. They’re predominantly designed for tasks that involve lifting materials to different heights and positions.
There are 3 main types of cranes that can be found in factories.
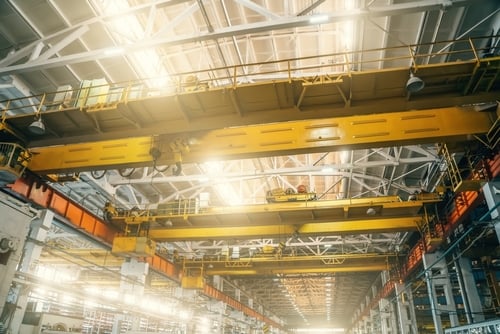
Overhead bridge cranes
Also known as overhead cranes, are the most common type of crane used in manufacturing environments like heavy plant and steel. The distinguishing feature of a bridge crane is its ability to traverse along a fixed track, supported by parallel overhead runways installed on either side of the working area.
Within the 'overhead crane' family, there are a number of different designs available, including a single girder overhead crane and double girder overhead crane systems.
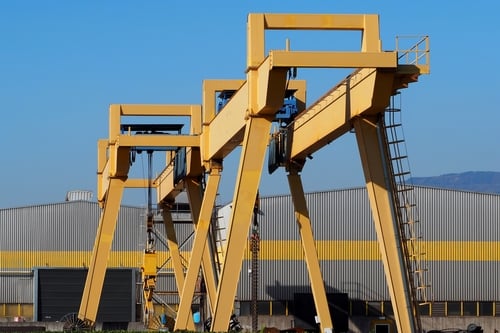
Gantry cranes
Gantry cranes are similar to a bridge crane system but with a distinct difference: they are supported by steel legs on the ground rather than being suspended from a building structure. These cranes are often used in outdoor settings, such as shipping yards, construction sites, and rail yards, where overhead support might not be feasible.
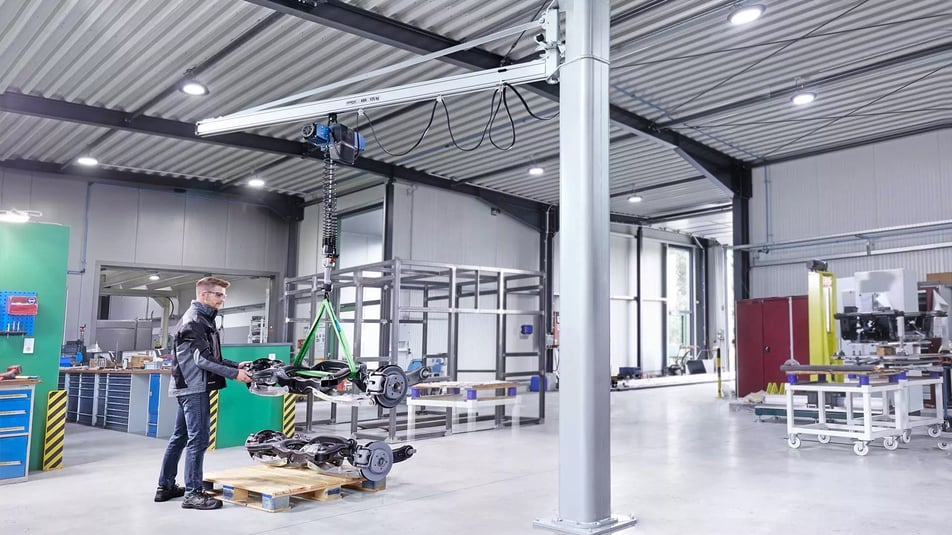
Jib cranes
Jib cranes are a compact and specialised crane systems that excel in confined spaces and workstations. They consist of a horizontal arm (jib) that pivots around a vertical mast. Jib cranes are commonly found in workshops, warehouses, and assembly lines.
Consideration 1: Efficiency – The Core Objective
Efficiency is a critical factor to consider when selecting material handling equipment. Businesses across every industry aspire to create streamlined processes that deliver optimum efficiency.
When it comes to selecting supporting equipment such as material handling solutions, any system should support efficiency objectives by maximising production output, optimising resource use and adapt to changing needs.
Electric Tugs Pros
Precise Control
Electric tugs offer excellent control, allowing operators to move heavy loads with precision, reducing the risk of accidents and damage.
Quick Deployment
With no complex setup required, electric tugs can be put to use immediately, maximising uptime.
No Operator License
Unlike overhead crane systems, electric tugs keep loads safely on the ground, meaning no operator license is required, increasing efficiency and enabling the just-in-time movement of loads.
Reduced Congestion
Electric tugs can safely and effectively transport materials through congested and tight areas, optimising space utilisation.
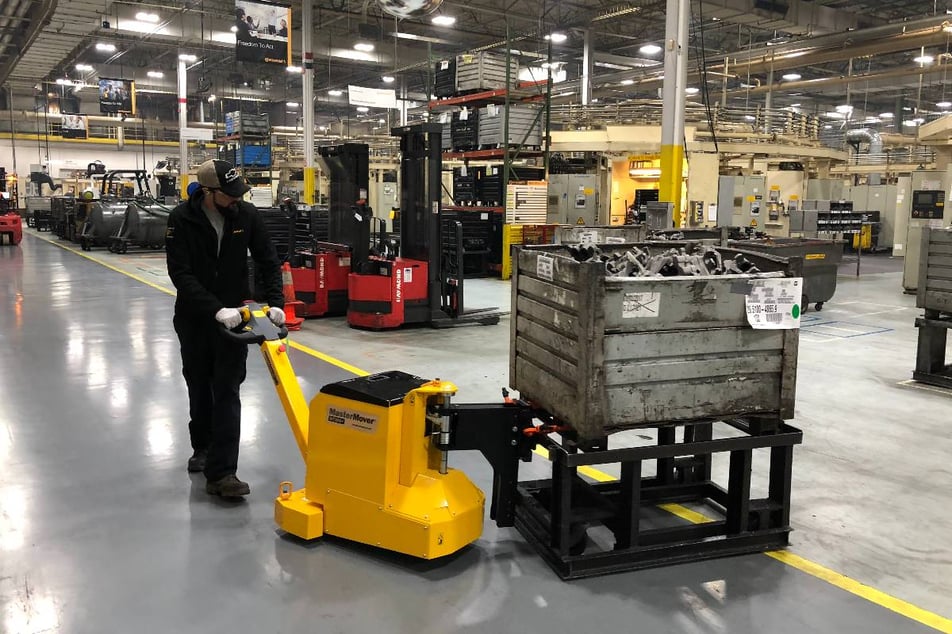
Electric Tug Cons
Load capacity
Most electric tugs are rated to handle a maximum load weight of 20,000kg. At MasterMover, our electric tugs can safely move loads of up to 30,000kg and beyond.
No lifting capability
Electric tugs offer an alternative approach to material handling when compared against overhead cranes. However, with a design focused on moving loads on castors, electric tugs cannot be used to lift heavy loads. Often, loads are placed on wheeled platforms by using other material handling solutions, with movement between locations then carried out through electric tug use.

Overhead Cranes Pros
High Load Capacity
Overhead cranes excel in handling heavy loads making them useful in heavy industries like construction and steel manufacturing. A wide range of cranes are available with lifting capacities up to 200 tonnes.
Vertical Lifting
Overhead crane systems offer vertical lifting capabilities, which can be an essential process in many manufacturing facilities.
Efficient in Larger Spaces
Overhead cranes are well-suited for larger manufacturing facilities with ample overhead clearance.
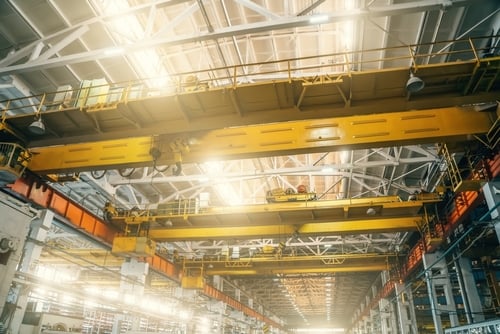
Overhead Crane Cons
Complex Installation
Setting up overhead cranes involves significant installation time and costs, potentially disrupting regular operations.
Limited Manoeuvrability
Overhead cranes are limited by fixed tracks. They can move loads from side to side on the lift bar tracks and lift and lower on the girders, but their design means they cannot move loads in all directions, limiting manoeuvrability.
Downtime and Availability
The fixed nature of overhead cranes can result in downtime. For example, a crane may be in use in another side of the factory. In its absence, operators must wait for the crane to become available before loads can be moved, resulting in downtime
Idle Time
Using cranes to lift heavy loads means comprehensive safety processes must be in place. If a load is being lifted, typically the area needs to be cleared to facilitate movement, increasing idle time.
Consideration 2: Flexibility – The Key to Competitive Advantage in Manufacturing
For the modern manufacturer, flexibility and the ability to pivot operations is critical to success. By creating flexible operations and processes, manufacturers are more resilient and better equipped to respond to factors such as supply chain challenges, economic downturns or increases in demand.
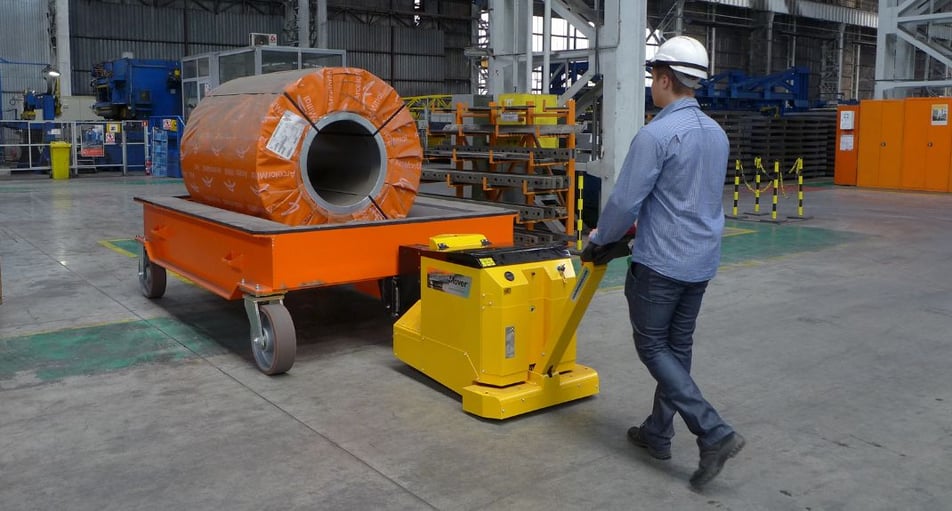
Electric Tugs
Moveable by their very nature, electric tugs deliver unparalleled flexibility. They can be used to adapt factory layouts and workflows, making them suitable for dynamic production environments where material flow needs to evolve rapidly.
Boasting a scalable design, electric tugs can be used to move a range of loads, likewise additional machines can be easily integrated to meet increased production output.
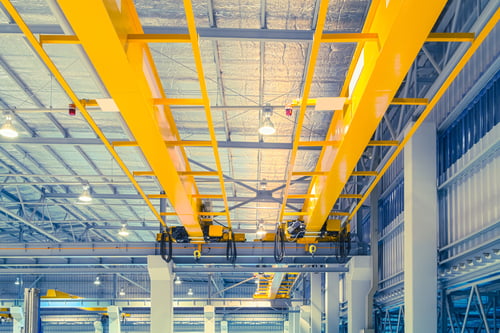
Overhead Cranes
While overhead cranes provide heavy-duty lifting capabilities, their flexibility is limited. Any changes to factory layout require adjustments to the crane's infrastructure, which can be time-consuming and costly.
Before investing in an overhead crane, it’s crucial that you audit and understand future plans as any modification or change can be a complex process.
Consideration 3: Cost – Weighing Up Cost Versus Return
As with any investment, cost is an important area to consider. When comparing material handling systems such as electric tugs and overhead cranes, you should weigh up initial investment costs, installation costs, maintenance and lifetime costs as well as assessing the potential return on investment.
Electric Tugs
Electric tugs are often far more cost-effective to purchase, install and maintain than overhead crane systems. Lower upfront costs, combined with minimal installation requirements, result in quicker returns on investment. Maintenance costs are generally lower, as electric tugs have fewer complex components.
Overhead Cranes
Unsurprisingly, overhead cranes come with much higher investment cost due to their complex installation process, which can often involve significant construction work.
It’s important to consider other costs aside from the initial purchase price – including, pre-installation building survey, installation, commissioning, downtime, load testing and training. Additionally, maintenance costs, especially for specialist parts and components, can be significant over time.
Project Snapshots
Every business is different which can make choosing the right material handling equipment challenging. It’s important to weigh up the pros and cons of any system and review them alongside your organisational objectives.
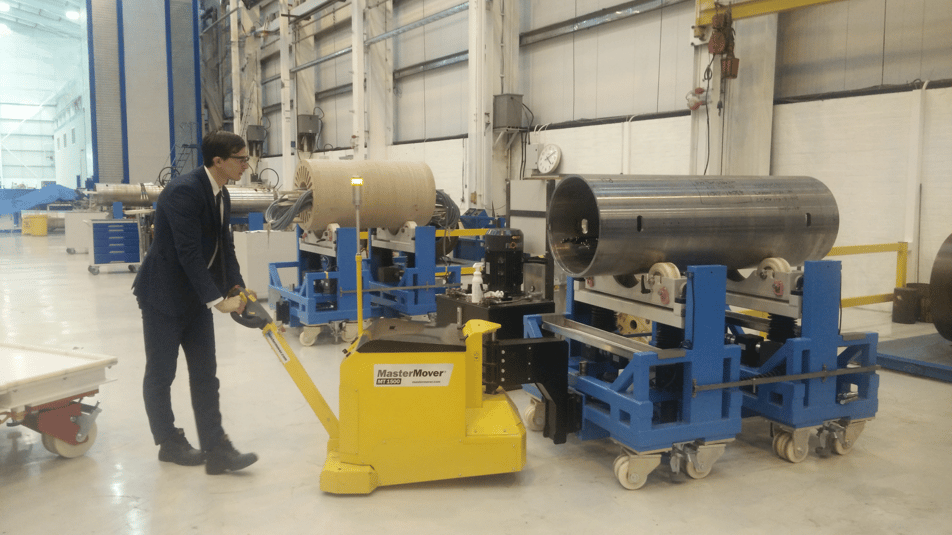
Hayward Tyler Cuts Overhead Crane Use by 50%
Hayward Tyler previously used an overhead crane to lift motors and pumps and lower them onto trestle frames. Individual or groups of engineers would then work on or add components to the motor/pump before it was transferred to a successive work station.
Transfers were frequent and would not always flow in the same direction. At sections where the two parallel overhead cranes did not meet, a forklift would need to be used to transport loads between cranes. This slowed the manufacturing process, reduced efficiency and increased costs.
Now, a MasterMover electric tug enables loads to be moved throughout the facility, increasing efficiency and delivering unrivalled flexibility.
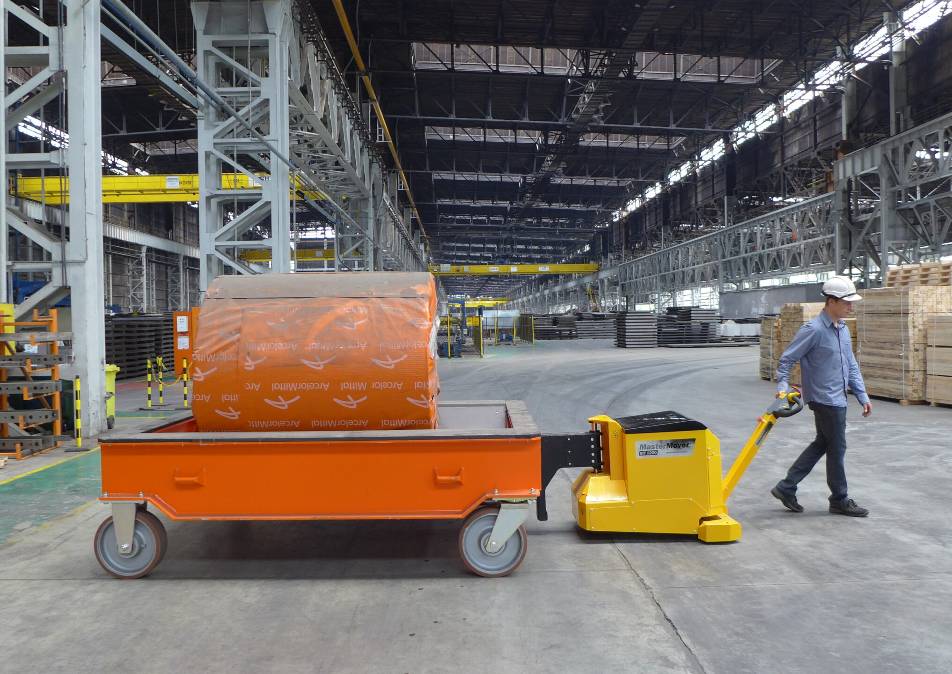
Steel Manufacturer Reduces Lost Time with Electric Tug
A leading steel manufacturer was using a lorry to move large metal plates from one assembly building to the next as the overhead crane system was only able to transfer the plates to the end of one building.
Although the buildings were adjacent, the layout of the factory meant that work in progress was loaded onto a lorry and then driven on a mile long circuit of the plant before being unloaded in the production hall next door.
By using an electric tug, the company virtually eliminated this lost time. A single pedestrian operator could move the load between the two buildings in minutes, using the tug to move a transfer trolley.
The ultimate guide to material handling
Material handling equipment
Looking to understand material handling in a little more detail?
We’ve compiled some helpful resources to get you started.
-
10 Principles of MHE
-
Advanced MHE
-
Best forklift trucks
-
Material handling in manufacturing
-
Forklift trucks vs electric tugs
-
Shunters vs electric tugs
-
Tow tractors vs electric tugs
-
AGVs vs Traditional MHE
-
A fork-free future
-
What is intralogistics?
-
Diesel forklift alternatives
-
Benefits of tugger trains
Choosing the Right Solution for Your Factory
When comparing electric tugs and overhead cranes, the right choice depends on the specific needs of your factory. Electric tugs offer greater efficiency, precise control, and flexibility, making them suitable for various industries and production layouts.
On the other hand, overhead cranes are the tool of choice where handling requires infrequent lifting over shorter distance, but their lack of adaptability and higher costs should be carefully weighed.
It Doesn’t Always Have to be a Trade-off
Ultimately, manufacturers must evaluate their operational requirements, future needs and budget considerations to determine whether electric tugs or overhead cranes will best support their material handling needs.
In many cases, a combination of both solutions provides the ideal balance of efficiency, flexibility, and cost-effectiveness for a seamless and productive factory environment.
Imagine a flexible factory...
If you’re looking to unlock greater operational efficiency and discover more flexible processes, we’re here to help. Speak to our team to discuss how electric tugs can revolutionise your operations.