Étude de cas : L'AGV optimise la productivité chez Toyota Motor Manufacturing
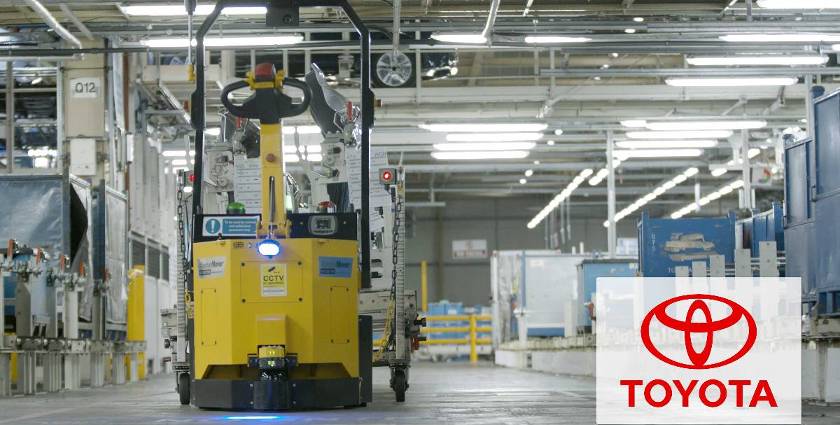
Toyota Motor Corporation a toujours été un pionnier de la fabrication industrielle, réputé pour son efficacité, sa production au plus juste et son innovation dans l'industrie automobile et bien plus encore.
Aujourd'hui, Toyota est la dernière entreprise en date à installer les systèmes de manutention automatisés de MasterMover pour améliorer l'efficacité et maximiser les performances de l'atelier.
Contexte du projet et identification des principaux enjeux
Les ingénieurs Toyota de l'usine de Burnaston, l'un des principaux centres de production du Royaume-Uni, ont identifié des lacunes dans leurs processus de production et de transfert des portes arrière en résine.
Avant, ces portes étaient chargées sur des trains de chariots pour faciliter les transferts dans l'ensemble de l'usine. Ce processus de transfert mobilisait un opérateur qui faisait continuellement des allers-retours tout en tirant des trains de chariots chargés tout au long de la ligne de production ; un processus à la fois inefficace et coûteux pour Toyota.
Avant la mise en place de notre AGV MasterMover, nous avions beaucoup de problèmes avec le processus de la porte arrière en résine. Un opérateur passait toute la journée à faire des allers-retours. C'était beaucoup de temps perdu pour Toyota.
Ryan OakleyIngénieur d'assemblage, Toyota
Auparavant, le processus de déplacement s'effectuait à l'aide d'un tracteur à conducteur porté et d'un chauffeur titulaire d'un CACES. Chaque équipe avait donc besoin de se voir attribuer des ressources dédiées au processus de déplacement. Considérant qu'il s'agissait d'une activité sans valeur ajoutée et d'une source de gâchis, Toyota souhaitait étudier la possibilité d'automatiser le processus de déplacement afin de maximiser l'efficacité.
Après avoir identifié le problème, Toyota a exploré les possibilités d'automatisation de ses processus de manutention en étudiant le marché.
Objectifs et Solutions
Les besoins principaux de Toyota ont orienté leurs critères de sélection, et ils ont identifié qu'ils avaient besoin d'un système AGV capable de :
Parcourir efficacement les locaux
Interagir et se joindre à d'autres activités de l'usine
Naviguer en toute sécurité dans les zones à forte fréquentation piétonne
Une évaluation approfondie des options disponibles a mené Toyota vers MasterMover, un fabricant de tracteurs pousseurs électriques ayant 25 ans d'expérience dans la mise en place de solutions de manutention efficaces.
La solution : AGV300 TOW
Toyota a choisi l'AGV300 TOW de MasterMover, une solution autonome permettant d'automatiser entièrement leurs processus de transfert des portes arrière en résine : voici pourquoi...
Une navigation de pointe pour une meilleure interactivité avec les processus existants
Doté d'un géoguidage intuitif, l'AGV300 TOW est conçu pour suivre un itinéraire prédéfini et assurer le déplacement répétitif de chariots.
Doté de la meilleure technologie de navigation du marché, l'AGV est programmé pour s'arrêter à des points de transfert spécifiques. Lorsqu'il atteint un point de transfert, l'AGV300 TOW envoie un signal au système de transfert des portes pour charger automatiquement les portes fabriquées sur les différents chariots.
Une fois le transfert des pièces terminé, l'AGV reçoit l'ordre de se déplacer vers la station suivante.
Répondre aux besoins fondamentaux des processus de transfert
En plus de la capacité à interagir avec les systèmes existants, tels que le système de chargement par transfert, Toyota avait besoin d'un système AGV capable de s'arrêter avec une extrême précision pour s'assurer que les pièces étaient correctement transférées sur le train de chariots.
"L'un des points clés du processus est que l'AGV doit pouvoir s'arrêter très précisément aux points de transfert et qu'il doit pouvoir le faire de manière très répétée". Kevin Jones, ingénieur principal, fabrication et assemblage.
La sécurité en standard
Si la productivité a été l'un des principaux moteurs du choix de l'automatisation, la sécurité n'était pas négociable pour Toyota.
Équipé de systèmes de sécurité de pointe, notamment de scanners au niveau du sol et en hauteur, ainsi que de systèmes d'arrêt d'urgence reliés entre eux qui permettent aux opérateurs d'arrêter le véhicule de n'importe où, l'AGV300 TOW est un gage de sécurité.
"L'AGV lui-même est équipé d'arrêts d'urgence et il se fixe également à notre train de chariots, qui est équipé d'arrêts d'urgence. L'appareil peut donc être arrêté de n'importe où le long du train". Kevin Jones, ingénieur principal, fabrication d'assemblages.
Grâce à sa technologie de navigation et de sécurité réactive, l'AGV300 TOW interagit de manière transparente avec les autres véhicules, tels que les tracteurs à sellette et les chariots élévateurs, et traverse en toute sécurité les zones fortement fréquentées. Sur son itinéraire très sollicité, l'AGV fonctionne 16 heures par jour et parcourt environ 8 000 km par an, livrant des portes arrière en résine tout au long du processus de production.
Nos opérateurs ont vraiment confiance dans l'AGV, en particulier en ce qui concerne sa sécurité et le fait qu'il fonctionne en parfaite harmonie avec eux et qu'il s'arrête si nécessaire. L'AGV fonctionne depuis environ deux ans et, pendant cette période, nous n'avons eu aucun incident de sécurité.
Ryan OakleyIngénieur d'assemblage, Toyota
Dépassement des attentes : Résultats et avantages pour Toyota
En place depuis deux ans, le système AGV300 TOW a permis à Toyota de rentabiliser son investissement, d'accroître son efficacité et de réduire ses pertes de temps. La mise en place du véhicule à guidage automatique (AGV) a permis à Toyota d'améliorer sa productivité et de réaffecter le personnel à des activités à plus forte valeur ajoutée.
"Le MasterMover a permis de rentabiliser l'investissement dès sa mise en service" Kevin Jones, ingénieur principal, fabrication et assemblage.
Un regard vers l'avenir pour Toyota et MasterMover
Toyota a confiance en la solution AGV300 TOW et en la qualité du service fourni par MasterMover tout au long du processus. Avec l'intégration réussie de l'AGV300 TOW, Toyota prévoit de déployer les systèmes AGV de MasterMover dans l'ensemble de ses processus de production à l'échelle mondiale.
"Je serais sans doute ravi de recommander le MasterMover AGV à d'autres entreprises désireuses d'automatiser leurs processus de manutention." Kevin Jones, ingénieur principal, fabrication et assemblage.
Avec 25 ans d'expérience dans la conception et la fabrication de solutions innovantes et fiables pour le déplacement de charges, les tracteurs pousseurs électriques MasterMover AGV offrent des performances élevées, reconnues par de nombreux clients dans le monde entier. Les solutions MasterMover AGV sont disponibles avec de nombreux systèmes de navigation pour répondre à vos besoins et déplacer des charges pesant jusqu'à 70 000 kg de manière automatisée.