Couplings & Connections
Material handling electric tuggers
Thank you for submitting your consultation request.
A member of the team will be in touch shortly.
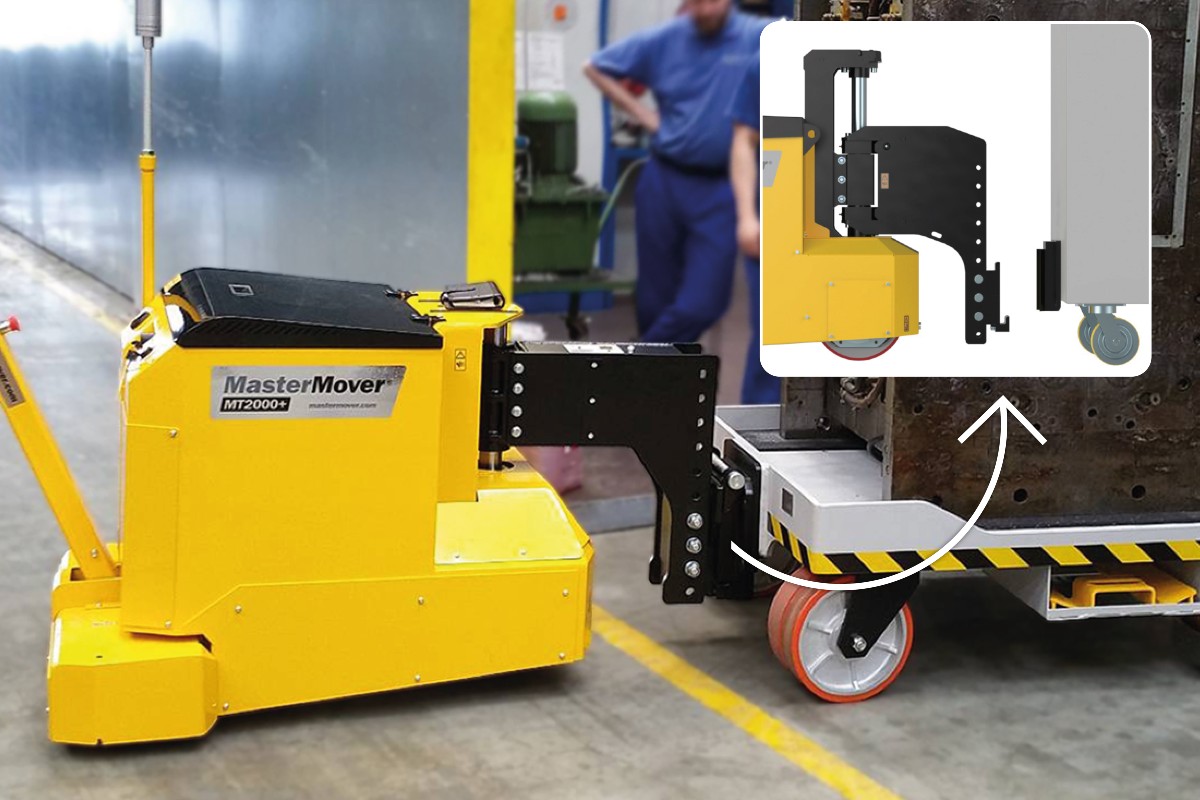
Couplings: The essential part of your electric tugger
When looking at material handling solutions, it’s important to consider how the equipment will connect to your load. Couplings are the essential part that facilitates this connection, and their design dictates how secure your equipment and load are during transportation.
Some people might be happy to compromise on the security of a coupling and its’ connection to the load when moving something like a 110 lbs. dumpster, but the same is unlikely to be true when moving 44,000 lbs. sub-assembly.
Couplings – small but mighty
When you work with a reputable tugger supplier, your application will be evaluated to specify the right tugger and coupling. Typically, in the scope of couplings, this assessment covers 3 areas; security, performance, and suitability.
While electric tow tugs and tows work with their corresponding couplings, couplings and their importance are often overlooked. Here’s why couplings are much more important than you think:
Security
A well-designed coupling will maintain a secure connection between the tugger and the load being moved. A poorly designed coupling might inadvertently ‘ let go’ of wheeled loads while in transit, the consequences of which could be serious.
Suitability
A well-designed electric tugger coupling will be quick and easy to connect/disconnect and will enable intuitive steering control over the load.
A poorly designed coupling might be hard to connect and disconnect which may create steering and control problems for the tugger operator.
Performance
For some machines, including our MasterTug range, couplings are fundamental in enabling the machine to move such heavy weights.
4 Types of coupling design on the market
Despite the variation in coupling designs on the market, most coupling offerings can be split down into four categories:
1. The Hook Design
The most common type of coupling on the market and often the default for many suppliers, the hook design as the name suggests, simply hooks onto your cart or cart’s frame
Simplistic in its’ design, many suppliers offer this in an array of dimensions but ultimately all of them function in the same way. While it delivers simplicity and to a degree, standardization – it’s important that you consider your environment, load, and operation, as hook designs have an element of movement and flex in their connection.
The biggest shortcoming of a hook-style design is that it risks ‘letting go’ of your load. If you have areas of uneven floor or need to navigate slopes or obstacles, a simple hook design likely isn’t the answer. As the tugger and load move around, fluctuations in the floor or movement on slopes can lead to the coupling inadvertently unhooking itself from your cart, resulting in a loss of control and the potential for serious consequences.
Basic hook designs don’t deliver a large amount of control when it comes to steering and handling a load either. This is because, without some kind of mechanical clamp, the hook can travel and move along your cart frame, making handling and control of the load difficult. This means that, particularly when pushing, the movement of the coupling on the cart frame might make steering and control harder than it needs to be.
Tip: An array of cost-effective simple hook options on the market allows you to connect and go, but if you’re looking for security and control, a hydraulic or mechanical clamp is a worthwhile investment.
2. The Bolt-on
Another type of coupling, and often our preference at MasterMover for heavier loads requiring added security, are couplings that are securely bolted onto your carts. These typically work by using a male (mounted on the electric tugger) that interlocks with a female (installed on your cart) to create a strong connection.
On our machines, this coupling configuration is essential to achieve the process of ‘weight transfer’, a clever way of transferring some of the load’s weight, through the coupling system down through the machine’s drive wheel – allowing it to gain traction, move and brake the load.
This type of coupling enables you to have an unbreakable connection to the load, move heavy weights, and provide you with maximum security and control of the load. However, the nature of this means a female coupling needs to be bolted or installed to each cart or platform you want to move. It’s important to consider the feasibility of installing multiple couplings on high volumes of carts or platforms and to weigh this up against the standardization it provides you with.
Our CombiCoupling system delivers powerful performance and guarantees complete control and maximum maneuverability.
Tip: Electric tugger suppliers should happily provide you with 3D CAD models of their coupling designs to enable you to review this alongside your existing equipment and review a suitable mounting point.
3. The Pin & Drawbar
A familiar design to many, typical towing connections such as pin couplings is perfect for loads already fitted with drawbars or towing eyes.
These offer a simple, standardized, plug-and-play option for applications where the bulk movement will be towing or pulling.
Other options in this category include couplings such as ball hitches and pintles. This connection point is commonplace in applications where existing tow units or forklifts have previously been used to mobilize loads.
4. The Custom Coupling
Where a standard solution isn’t suitable, an experienced supplier will work with you to assess if a customized coupling can be designed. Situations where this often arises are where you may have a high quantity of carts that can’t be modified, no obvious connection point, or where there are space restraints on your cart.
A custom coupling design is often seen as an attractive option in these situations, or when the task of modifying a range of carts to achieve standardization seems too difficult.
However, this approach should be viewed with caution and carefully considered. As with anything custom, custom coupling designs typically come at an increased cost and lead time and there is nearly always a trade-off in creating a multifunctional coupling design. Cost, ease of use, and performance are all areas where a custom design might demand compromise.
The other risk with creating a unique custom coupling is that it hasn’t been tried and tested. Custom couplings cost time and money and so, if possible, it’s better to push for a standardized cart design. However, for many manufacturers with specialist set-ups, custom couplings are essential to facilitate connection where unique processes or requirements dictate that modifying carts isn’t feasible.
Where a custom coupling is required, it is important to make sure you’re working with a supplier who’s up to the task. At MasterMover, we have a Customer Engineering team dedicated to creating custom solutions to complex connection requirements. With 25 years of industry knowledge, we’ve built a proven track record in designing customized couplings for customers across the globe.
Tip: If you’ve assessed that a custom coupling is required, it’s important that when working with a supplier to design a custom connection that full technical data is provided and accurate to make sure any proposed coupling is designed correctly.
Couplings are important in any application, but as the weights get heavier, they become even more crucial.
Lesley LaneUK Sales Manager, MasterMover
The ultimate guide to electric tuggers
Electric tugger essentials
Looking to understand electric tuggers in a little more detail?
We’ve compiled some helpful resources to get you started, covering everything from how they work, different types of batteries, getting the right connection point and more…
-
What is an electric tugger?
-
5 benefits of electric tuggers
-
Do you need a license?
-
How electric tuggers work
-
Batteries & charging guide
-
Castor wheel explainer
-
Frequently asked question
-
Why businesses use electric tuggers
-
Pedestrian operated vs remote control
-
Automation & remote control options
-
Tuggers vs tows
-
Pricing guide
-
Walkie tuggers
Choosing the right coupling
If you’re wondering how you select the right coupling, the truth is, there isn’t a definitive ‘pick this one’ answer. At MasterMover, we work with you to specify the most suitable coupling for you – considering an array of factors on a case-by-case basis.
However, as a customer or user, here are 3 things to keep in mind when looking at couplings:
Simplicity
Overcomplicated designs often compromise operator comfort and ease of use.
Achieving a balance between fit-for-purpose and simplicity can be difficult when couplings are being designed around specific applications. However, one way this can be mitigated is by involving the people who’ll be using the equipment in the design discussions.
Standardization
Taking cues from Lean methodologies, standardization, where possible, minimizes the room for error and variation.
Standard couplings provide a tried and tested solution that, if configured correctly will deliver guaranteed performance. If your operations allow, a standard solution should always be the first point of call before assessing a customized option. If this can’t be achieved, ensure you’re working with a supplier asking for detailed information on your application.
Scalability
When looking at couplings, it’s important not to pigeonhole your needs.
In manufacturing, processes change, and production requirements fluctuate. Ensuring any coupling you introduce can be scaled up and installed on additional carts maximizes your return on investment and enables you to future-proof your handling processes.
While the topic of couplings may not be the most exciting, it is important that you consider this small, but critical part when looking into electric tugger solutions. If your chosen supplier isn’t asking the right questions about your processes and equipment, the chances are, the coupling has been overlooked and it’s time to walk away.
The correct coupling keeps your equipment secure and facilitates complete control and movability of your equipment.
We're here to help
If you’re looking to improve safety, remove the risk of injury and unlock greater operational efficiency, we’re here to help. Speak to our team to discuss your application.