7 Steps to Retrofit Your Warehouse for Cart Tuggers
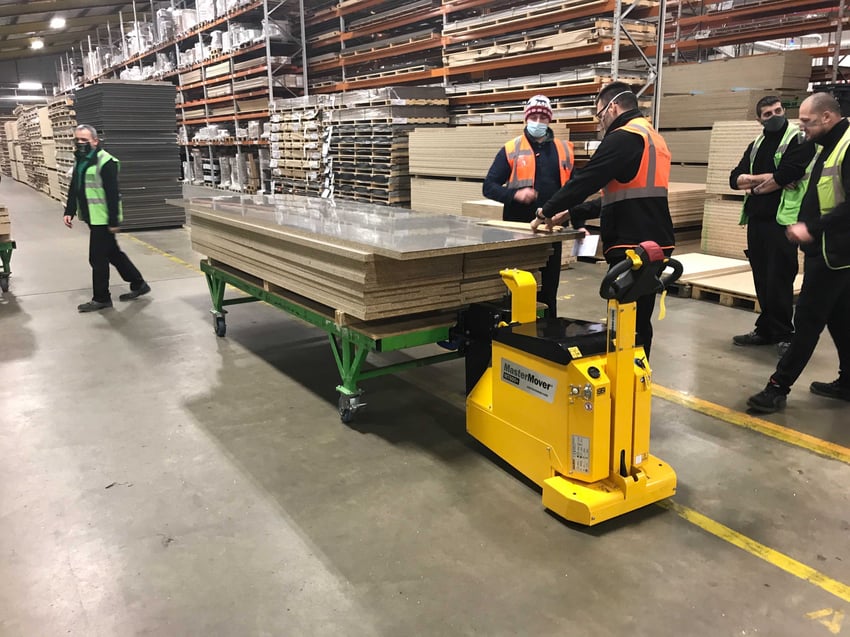
This guide is designed to assist with retrofitting your warehouse for cart tuggers, with the overall goal of replacing traditional forklifts. It offers a roadmap to help you navigate each critical step, from assessing your current setup to seamlessly integrating electric warehouse tuggers into your daily operation.
Through this guide, you'll gain valuable insights, practical tips, and considerations that will ensure a successful transition. Whether you're a warehouse manager aiming for operational improvements or a business owner looking to boost efficiency and sustainability, this guide equips you with the knowledge needed to make informed decisions and execute a successful warehouse retrofit.
So, let's embark on this journey to explore the world of cart tuggers and how they can transform your operation.
1. Assess Current Warehouse Infrastructure
Before diving into the process of retrofitting your warehouse for cart tuggers, it's essential to have a clear understanding of your current warehouse setup. This step is the foundation upon which you'll build your retrofitting plan.
Here's how to get started:
Conduct a Thorough Inventory Assessment
Begin by taking a comprehensive inventory of your warehouse's current state. This includes:
Identifying Existing Equipment:
Document all equipment currently in use, particularly forklifts. Note their make, model, and condition.
Analyzing Layout and Floor Plan:
Review your warehouse's layout and floor plan. Consider factors like aisle width, storage shelving, and any obstacles or bottlenecks that may affect material flow.2. Evaluate Current Workflow and Material Handling Processes
Next, evaluate your existing workflows and material handling processes. This involves:
Workflow Mapping
Document the journey of goods within your warehouse, from receiving to storage, picking, and shipping. Identify any inefficiencies or areas where the current system falls short.Pain Points and Bottlenecks
Pinpoint pain points and bottlenecks in your operations. These could include delays in loading/unloading, congestion in high-traffic areas, or difficulty maneuvering around tight spaces.Identify Areas for Improvement
Finally, consider the specific challenges and areas where improvements are needed. These may include:
Safety Concerns
Note any safety issues associated with forklift operation, such as accidents, damage to goods, or near-miss incidents.Environmental Impact
Assess the environmental impact of your current equipment, including emissions and energy consumption.Efficiency and Productivity
Evaluate the overall efficiency and productivity of your warehouse. Are there time and resource-saving opportunities?Why This Assessment Is Crucial?
Conducting a thorough assessment of your warehouse set-up is necessary as it provides the baseline data needed to make informed decisions about adopting warehouse tuggers. Understanding the strengths and weaknesses of your existing setup helps tailor your retrofitting plan to your warehouse's specific needs.
With this assessment complete, you're now ready to move on to the next steps in the retrofitting process, including understanding the requirements of electric warehouse tuggers and budgeting for the transition.
3. Understanding Electric Tugger Requirements
Now it's time to dive into understanding the specific requirements of cart tuggers. These requirements will play a crucial role in determining how to adapt your warehouse for this innovative material handling solution:
Exploring the Capabilities and Advantages of Electric Warehouse Tuggers
To begin, let's explore why cart tuggers are gaining popularity as an alternative to forklifts:
Maneuverability
Electric cart tuggers are known for their exceptional maneuverability. They can navigate tight spaces and congested areas with ease, making them well-suited for warehouses with narrow aisles.
Versatility
Electric cart tuggers are versatile and can be used for a variety of tasks, from towing materials to transporting goods within a warehouse.
Safety
Electric cart tuggers often come equipped with advanced safety features, reducing the risk of accidents and improving overall warehouse safety.
Energy Efficiency
Compared to traditional forklifts, cart tuggers are more energy-efficient, reducing operating costs and environmental impact.
4. Determine the Specific Needs of the Integration
When preparing to retrofit your warehouse for electric tuggers, several factors need your attention. First, determine the load capacity your electric tugger cart will need to handle. This calculation serves as the foundation for defining the tugger's power and capacity requirements, ensuring that it can efficiently and safely transport the materials or goods within your warehouse.
Another consideration is the power source and charging requirements for your cart tuggers. This involves not only deciding where the charging station will be located but also assessing whether your warehouse's electrical infrastructure can support the additional power demand. Adequate planning ensures that your cart tuggers remain operational without unnecessary interruptions.
Maneuverability and space considerations are essential to a successful retrofit. Given the fact that forklifts are currently being used in your warehouse, it’s probably safe to assume your warehouse layout will support the movement of cart tuggers.
How Cart Tuggers Differ from Forklifts in Terms of Infrastructure Needs
Cart tuggers have distinct requirements compared to forklifts. You'll need to have a dedicated area to park the electric tuggers and available outlets to charge the battery. Electric cart tuggers only require a standard outlet for ease of charging.
5. Create a Budget & Identify Potential Cost Savings
Once you've estimated the costs, create a detailed budget that accounts for each expense. Be sure to include:
Capital Allocation
Determine how much capital you can allocate to the retrofitting project. This may involve seeking funding or financing options if necessary.Return on Investment (ROI) Analysis
Perform an ROI analysis to understand when you can expect to start seeing cost savings and recouping your investment.Cart tuggers offer several potential cost-saving advantages over traditional forklifts:
Energy Efficiency
Cart tuggers are battery-operated so fuel is not required.Lower Maintenance Costs
Cart tuggers typically have fewer moving parts and require less maintenance than forklifts, leading to lower maintenance expenses.Reduced Labor Costs
With no operator license required, any employee, with little training, can operate a tugger cart.6. Choose the Right Electric Cart Tugger
Consider your warehouse's specific requirements, including load capacity, operational space, and the types of materials or goods you handle. MasterMover will discuss your requirements and provide expert guidance on selecting the most suitable models. Both compact electric tuggers and heavy-duty electric tugger are available. Once the model is selected, MasterMover can provide a demonstration of the machine.
7. Integrate Cart Tuggers into Your Warehouse Operation
It’s time to train the team! Since cart tuggers are quite simple to operate, training won’t take a great deal of time. You’ll want to provide instructions on controls, maneuvering, and safety procedures.
By following these steps, you'll be well-prepared to integrate cart tuggers into your warehouse operations. As you optimize your workflows and take advantage of the efficiency gains they offer, you'll be on your way to realizing the full potential of this innovative material handling solution.