How to reduce manual handling injuries + Checklist
Manual Handling
Uncover the essential strategies for maintaining a safe and manual handling injury-free workplace. We explore the pivotal role played by ergonomic equipment and comprehensive training in mitigating manual handling injuries - plus, get a free manual handling checklist!
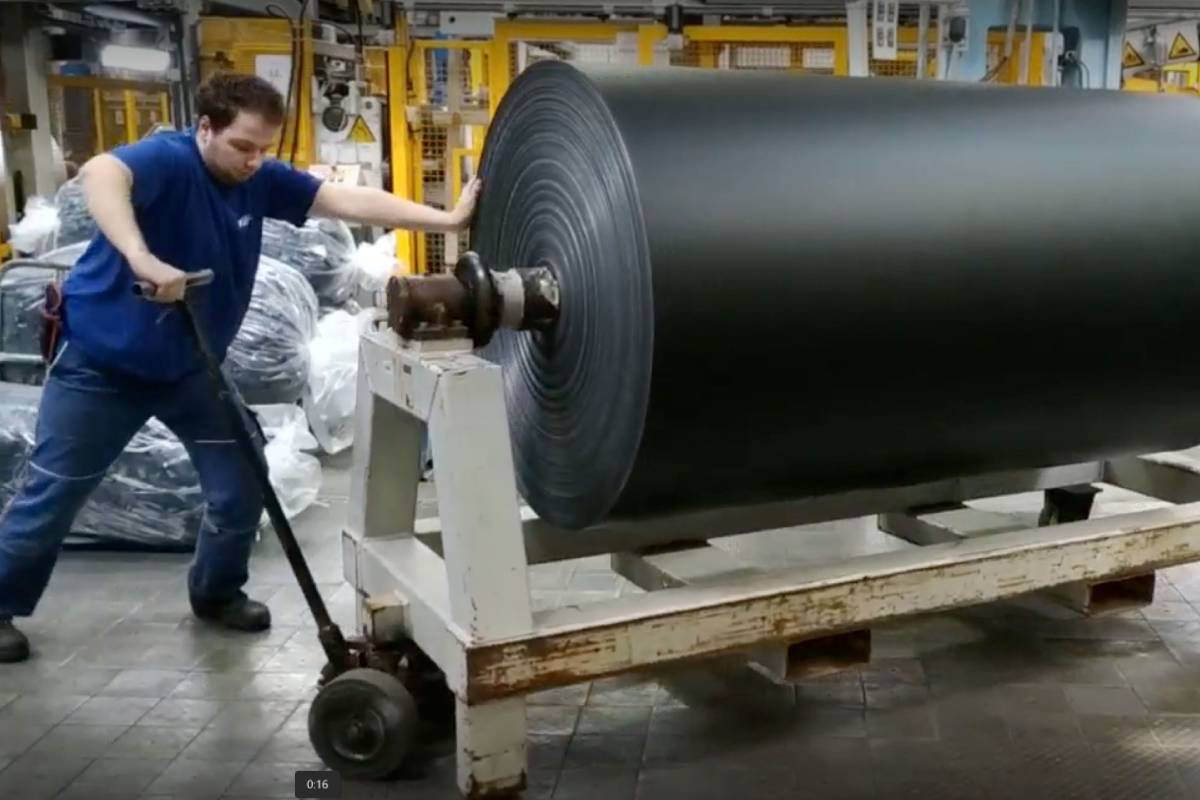
Manual handling injuries are common in manufacturing industries and can have devastating consequences for workers and manufacturers. Manual handling injuries can significantly reduce productivity and quality of life if left unchecked.
That’s why manufacturers need to understand what manual handling is, identify its associated risks, and develop strategies to reduce those risks.
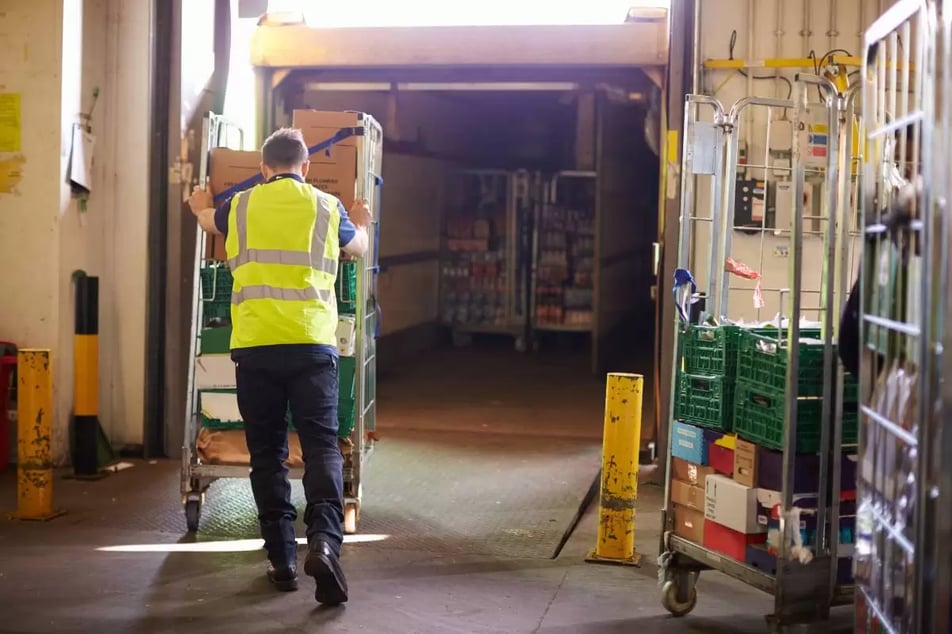
What is manual handling?
Manual handling covers various activities such as lifting, pushing, pulling, lowering, and positioning loads, equipment or parts.
Common tasks include lifting boxes or pushing heavy-wheeled loads up and down inclines.
What are the risks of manual handling?
Hazardous manual handling operations present several risks. Incorrect manual handling can result in serious injuries and manual handling incidents within the workplace. The likelihood of manual handling injuries increases when:
- Tasks are repetitive
- Operations exceed an employee’s abilities (i.e., weight being moved)
- The layout of tasks is awkward
- Employees have existing injuries
Manual handling can lead to musculoskeletal disorders (MSDs), back injuries from overexertion, strains from awkward posture and even hernias from overexertion. Other risks include trips and falls caused by uneven surfaces or poor visibility when moving materials.
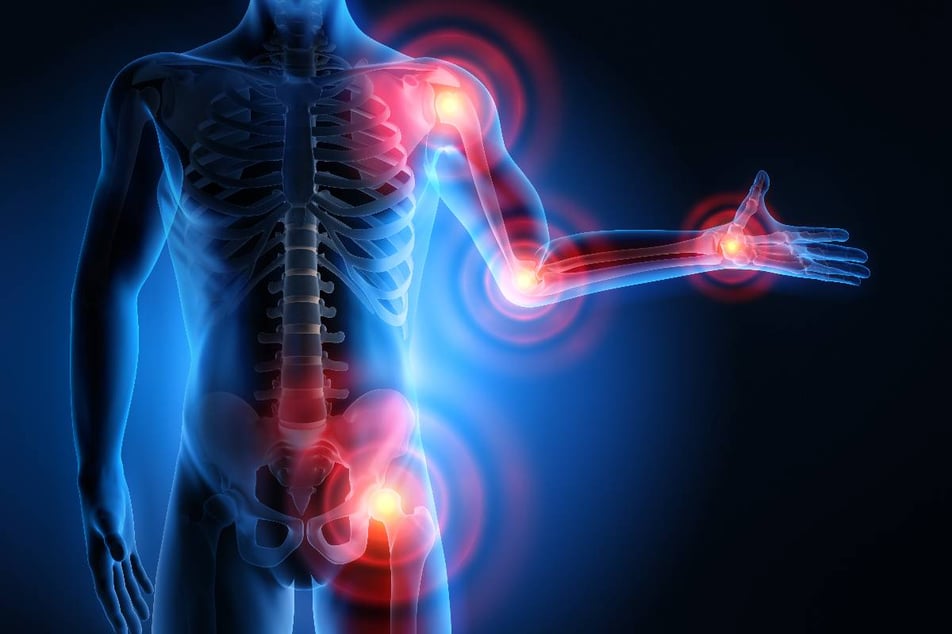
Which manual handling activity is most hazardous?
Different types of manual handling activities carry different levels of risk depending on their complexity, frequency, and difficulty.
The most hazardous manual handling activity requires the repeated movement of heavy loads in awkward positions. Such tasks present a high risk for MSDs because muscles have no time to rest between movements.
5 Common manual handling injuries in the workplace
-
1. Back Injuries
-
2. Musculoskeletal Disorders (MSDs)
-
3. Strains and Sprains
-
4. Hernias
-
5. Slips, Trips and Falls
1. Back Injuries
Back injuries are the most common injury caused by manual handling. Often injuries are caused by lifting heavy loads but pushing and pulling wheeled loads, poor posture or repetitive movements are also key contributors.
2. Musculoskeletal Disorders (MSDs)
Repetitive movements, over-exertion, lifting, pushing, and pulling heavy trolleys are just a few aspects of manual handling that can lead to MSD in the workplace.
3. Strains and Sprains
Strains and sprains occur when musculoskeletal tissues become overloaded from activities such as moving loads that are too heavy or by using excessive strain when gripping.
4. Hernias
Overstraining to lift, push, pull or stop a heavy load through manual handling can cause hernias.
5. Slips, Trips and Falls
The manual movement of heavy loads can increase the risk of slips and trips through poor visibility or movements on uneven floor surfaces.
Compensation Claims for Manual Handling Injuries
When injuries occur due to manual handling, affected individuals have the right to seek compensation for their damages and submit an injury claim. Compensation claims are filed against employers and aim to cover medical expenses, rehabilitation costs, lost wages, and other related damages.
On average, compensation amounts for a manual handling claim can range from $1,080 to $42,000*, depending on the severity of the injury.
Your Guide to Tackling Manual Handling
Manual Handling
Explore our comprehensive manual handling resource hub—expertly curated materials designed to enhance workplace safety. Elevate your knowledge and empower your team to prevent injuries, making your workplace safer and more efficient.
7 ways to reduce manual handling risks and workplace injury
To reduce manual handling risks in manufacturing environments, there are several strategies employers can implement, including
1. Use a mechanical aid
Incorporating appropriate mechanical aids into your process can make tasks easier on staff, i.e., lifting equipment to take the weight when lifting load or electric tuggers to take the strain out of moving wheeled loads. A range of handling equipment is available to reduce manual handling incidents, including mechanical lifting aids, ergonomic trolleys and other material handling equipment.
2. Identify any hazards with a manual handling risk assessment
Regularly reviewing your processes and tasks with employees will help identify manual handling tasks with a higher risk of injury.
3. Proper job design
This involves ensuring that jobs and work processes are designed with safety at the forefront and avoid manual handling where possible.
4. Appropriate manual handling training
Ensure employees receive adequate training for each task, how to carry out manual handling activities safely and on correct manual handling techniques.
5. Keeping track of workloads
Monitor how much each worker is doing and what tasks involve manual handling and excessive physical exertion.
6. Regular breaks
Give employees scheduled breaks throughout their shifts, so they have time to rest between tasks.
7. Assess individual abilities
Evaluate each employee’s capabilities during risk assessments so you know if particular staff members require additional support/mechanical aids when performing specific tasks or if they are at higher risk of injury.
Download your manual handling injury checklist
Implementing safe manual handling preventative strategies creates an environment where workers feel safe, resulting in fewer workplace injuries and manual handling accidents, reducing staff absences, and improving productivity overall.
We’ve created an easy-to-use checklist to help you quickly assess manual handling processes and identify the next steps in reducing the risk of manual handling injuries.