AGVs – The key to modular production in automotive manufacturing
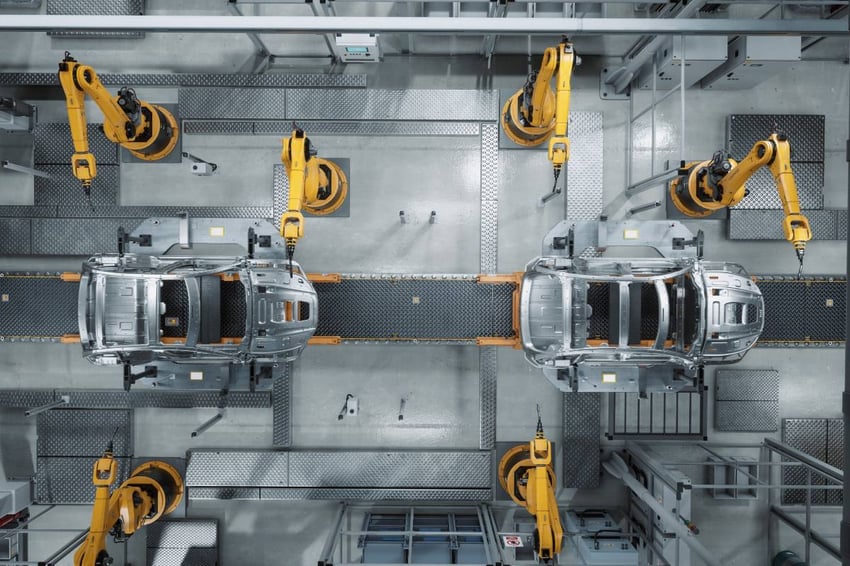
Modular manufacturing and autonomous solutions will drive the automotive factory of the future, here’s how…
The first assembly line revolutionised the automotive industry, enabling the mass production of standardised products. However, today’s automotive manufacturers are dealing with greater complexity and variation, pushing the limits of the conventional assembly line.
This is increasingly the case as manufacturers expand the production of electrified powertrains alongside the manufacture of ICE vehicles, resulting in bottlenecks, reduced productivity and increased costs.
To respond to this challenge, many automotive manufacturers are looking to move towards more flexible, modular manufacturing systems. This move is enabled by new advances in automation technology in AGV systems – enabling manufacturers to improve efficiency while reducing waste.
In this blog, we discuss:
Flexible, modular automotive manufacturing – What is it?
The concept of modular manufacturing seeks to utilise workstations in a set sequence to allow products to be produced most efficiently and in parallel.
This aligns with lean techniques and centres around optimising continuous production flow from one cell to another whilst supporting product variation.
What are the benefits of modular automotive assembly?
Modular cells are not dependent on each other, which enables automotive manufacturers to minimise any wasted time. Downtime in one cell has minimal impact on the entire production process, unlike a traditional conveyor-driven production system.
This approach enables manufacturers to modify cell set-up, adding in or removing cells where required – increasing their ability to respond and react to changing market dynamics.
Within lean manufacturing, a core waste is worker underutilisation. A modular cell production system enables manufacturers to mitigate this, with a study by the Boston Consulting Group showing that cell manufacturing improved worker utilisation by 12%.
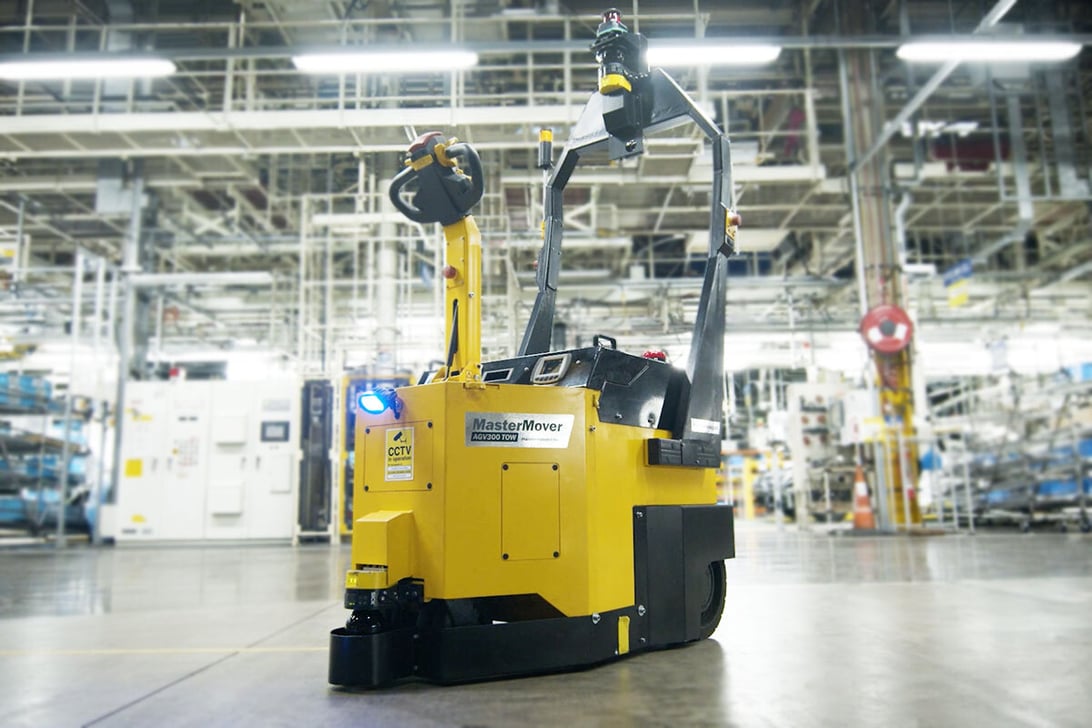
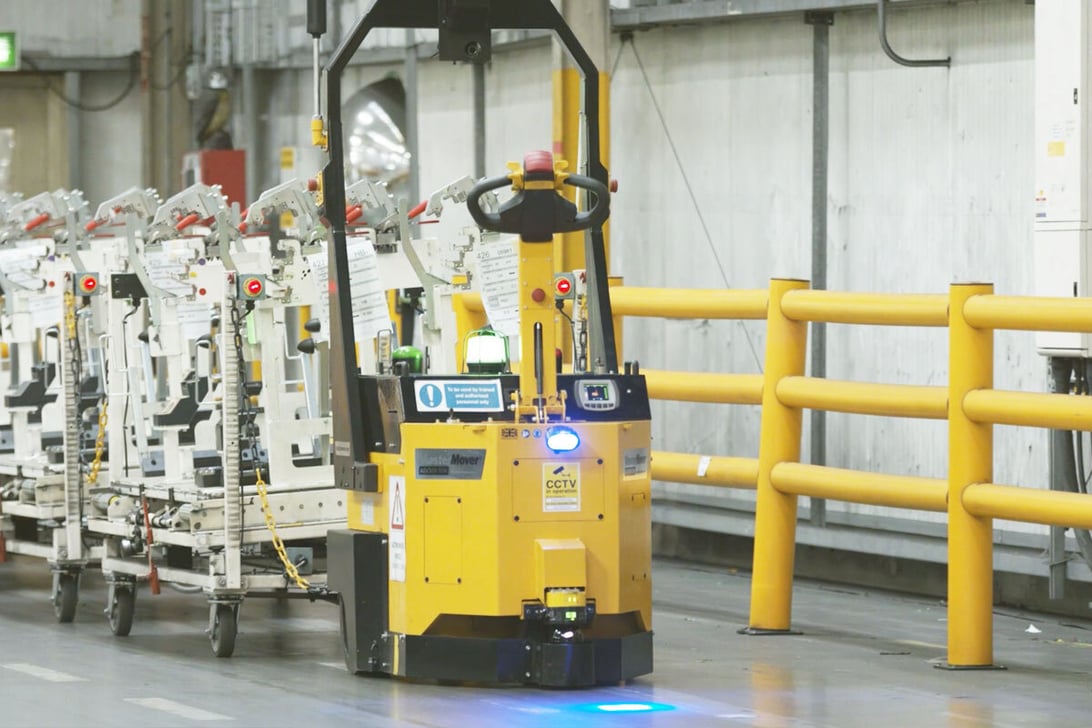
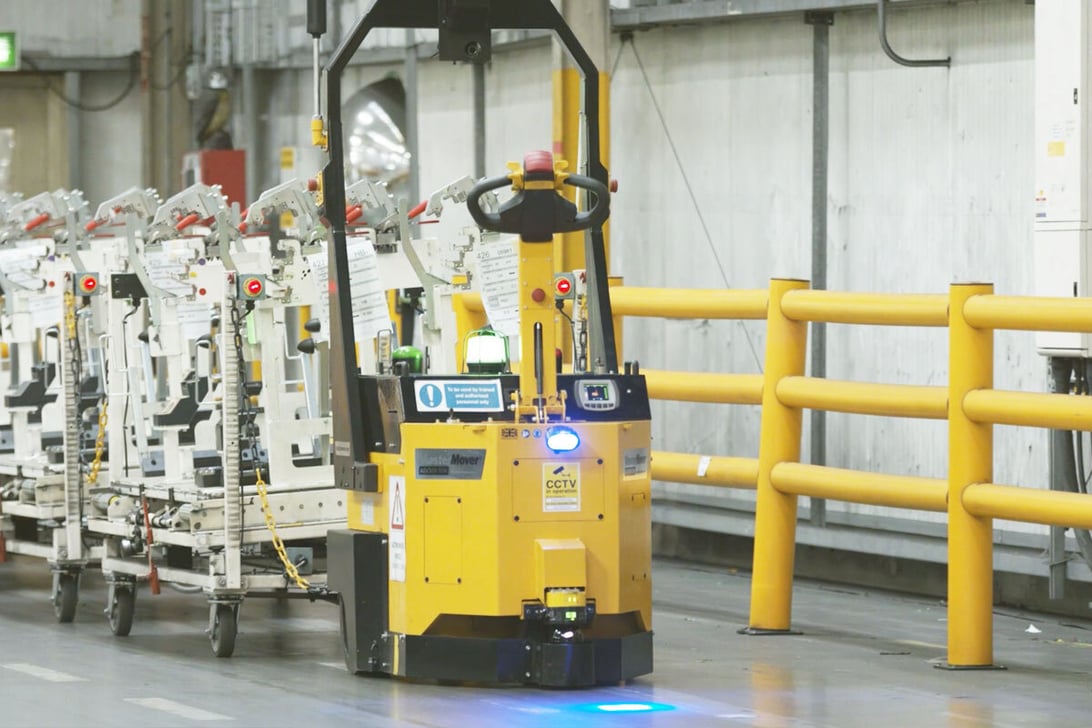
.jpg?width=1460&height=728&name=AGV_Still-1.18-Image_1200x800px%20(1).jpg)
How do Automated Guided Vehicles fit into this system?
Automated Guided Vehicles play a vital role within modular production systems, replacing the traditional conveyor design in many operations.
With the acceleration of Industry 4.0 technology in automotive factories, AGV systems can interact with factory infrastructure to gain dispatch commands and reroute to specific cells or workstations in line with production needs. Likewise, a modular production system allows AGVs to transport sub-assemblies and parts without being influenced by the next step in the assembly process.
What types of AGV systems are available?
AGV electric tugs are available with two core navigational systems – Line Follow and Natural Navigation.
Line Follow AGVs are already a familiar system for automotive manufacturers but, the rapid innovation seen in Natural Navigation technology means AGVs can now operate with an increased level of autonomy and flexibility – perfectly suited to the needs of automotive production.
Line Follow
Set to follow a defined path that can be specified by the operator. Line follow capabilities make sure AGVs follow the same route time after time, even when working in tight spaces or moving loads through areas with minimal clearance.
Barcodes can also be placed on the ground, or other similar identifiable prompts, for the machines to scan for additional programmed information, such as slowing down through a specific area. This makes the environment safer and reduces the risk of damage to high-value loads, the premises, and people.
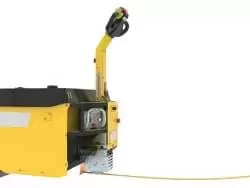
Natural Navigation
The most sophisticated form of AGV, natural navigation machines use sensors and scanning systems to navigate autonomously by detecting and mapping the environment around them to move around obstacles.
The sensors ensure a programmed response to any detected risk and the units will stop until the hazard has been moved away.
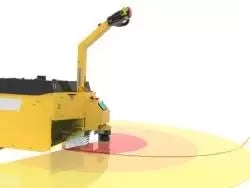
AGV in Action: Toyota
Learn how Toyota Motor Manufacturing used an AGV system to automate its driving processes.
A world-leader in its field, the automotive manufacturer has achieved return on investment and improved operational efficiency when moving parts to the production line.
Value-adding
AGV systems empower staff to focus on value-adding tasks – beyond the simple movement of materials – driving additional ROI and efficiency.
Scalability
AGVs offer manufacturers a scalable material handling solution that can interact with Fleet Management and Warehouse Systems to anticipate requirements and take commands.
Speed & Accuracy
AGVs can transfer parts from one area to another with greater speed and accuracy than both manual handling approaches and alternative material handling solutions – reducing the risks associated with human error during tedious tasks such as moving body panels from one cell to another.
The key to flexible production
Automated Guided Vehicles are becoming an essential element of the modern automotive manufacturing process.
Combining intuitive AGVs with modular production systems offers unrivalled flexibility, particularly as manufacturers grapple with product variation and complexity.
With their inherent potential for scalability and reliability, AGV systems provide excellent opportunities for increasing efficient operations for automotive manufacturers.
So, if you’re looking for a safe, reliable automation system that increases your operational efficiency while unlocking greater versatility in your manufacturing operations then AGV electric tugs might be right for you.