Looking East: Challenges & Opportunities in Asia’s Biopharma Industry
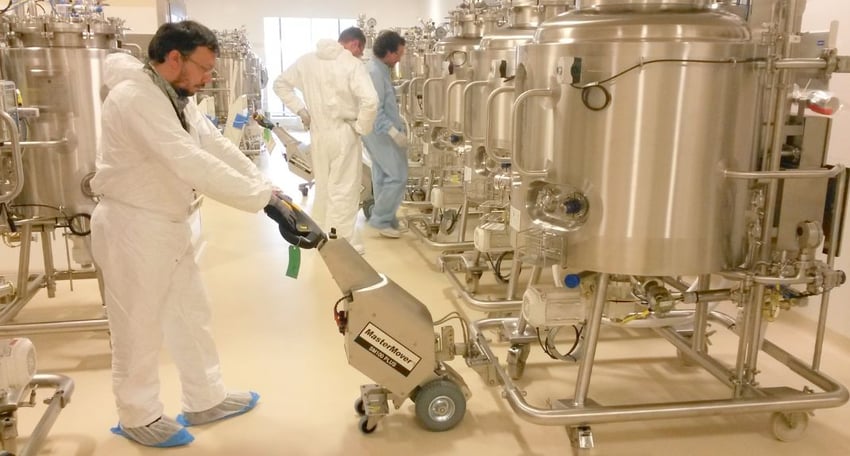
In recent years the biopharma has been a central focus worldwide. An increased effort in vaccine development turned previously lesser-known manufacturers into recognisable household names.
The previous pressure to develop vaccines triggered substantial investment and innovation globally but particularly in Asia. Whilst much of the region has historically been well-known for low-cost drug manufacturing, over the last decade, the region has shifted its’ image to focus on becoming more agile, innovative, and capable of much more complex production and development.
The trends within Asia’s biopharmaceutical industry come as no surprise to most, especially considering its rapid growth and dynamic nature. The region boasts an extensive and innovative hub for biopharmaceuticals, while differing markets within Asia present unique opportunities for MasterMover, the following are key areas to watch:
1. Japan
Updated information reflects Japan's continued strength in pharmaceutical production and innovation. As of 2022, the production value of pharmaceutical drugs in Japan reached approximately 9.98 trillion Japanese yen, reflecting a slight increase from prior years, despite challenges like an aging population and shifts in global markets.
Japan also maintains its position as a global leader in pharmaceutical innovation. It consistently ranks among the top nations in research and development (R&D) expenditure within the sector. For example, Takeda Pharmaceutical, one of Japan's leading firms, invested over 633 billion yen in R&D as of 2023, underscoring the emphasis on advanced drug development.
2. China
With a market value of $93 billion in 2020, and an expected value of US$117.50bn in 2024, China is well-embedded within the strategy of most western multinational organisations.
As it moves to shift away from high-volume, low-value production, China continues to be home to an expanding array of domestic manufacturers and CDMO’s.
3. India
In terms of volume, India supplies approximately 20% of worldwide pharmaceuticals and is one of the fastest growing markets globally. Generic drugs make up a significant share of India’s growing market and the country ranks 3rd globally for production volumes.
4. Singapore
Despite its small geographical footprint, Singapore is a powerhouse in biopharmaceutical manufacturing, hosting facilities for eight of the world's top ten pharmaceutical companies. By 2022, the country had expanded its capabilities in biologics and advanced therapies, with biopharma manufacturing contributing significantly to its economy. Singapore's strategic location, robust intellectual property protections, and world-class R&D ecosystem make it a critical hub in Asia for life sciences innovation.
Leading biopharma companies in Asia are still leveraging lessons from the COVID-19 pandemic to position themselves as strong competitors and strategic partners globally. Trends such as digital transformation, supply chain restructuring, regulatory modernisation, and the localisation of production remain central to the region's evolving biopharma landscape. We have seen that making processes flexible is vital not only for manufacturers, but also for biopharma development sites.
Supporting your move to flexible production, safely
Throughout the biopharmaceutical industry, the growth of single-use systems has accelerated. Simply put, the main aim of single-use systems is to save time and ultimately money. This, coupled with the need for flexible manufacturing has led many of Asia’s key players to move towards more mobile and flexible processes. For most, this has meant a shift towards wheeled process equipment which in turn, presents its’ own challenges.
Here’s three project snapshots from across Asia where customers have looked to solve the challenges of flexible production with our cleanroom-ready tugs:
1. Safer transfers
Machine: MT5-400+ SS IP 55
Country: China
Load: Chromatography Columns
Typically, moving away from fixed equipment in pursuit of more flexible operations means installing wheels onto processing equipment. As most Safety Managers will testify, just because a 3,000 kg chromatography column has wheels, it doesn’t mean that processing staff should be moving it by hand.
A new pharmaceutical factory in Shanghai wanted a way to move their chromatography columns without compromising safety or flexibility. Our MT5-400+SS offered the perfect solution, allowing staff at the facility to safely move the columns without the risk of injury and with the secondary benefit of efficiency gains.
2. Precision manoeuvrability
Machine: SM100+SS
Country: Japan
Load: Process Tanks
When looking for material handling equipment, balancing the regulatory requirements of production alongside efficiency and staff safety is difficult at the best of times. Add into that tight spaces and large high-value equipment and it becomes incredibly difficult.
After assessing countless options, a capsule manufacturer in Japan contacted MasterMover after struggling to find a solution compact enough to move large tanks around a tight production area. With a compact footprint of less than 0.5m², the SM100+SS is allowing staff to precisely move the tanks – reducing the risk of costly damage to equipment.
3. Quicker configuration turnarounds
Machine: MT20/960+SS
Country: China
Load: Chromatography Columns
The core aim of flexible facilities for manufacturers is quicker suite changeovers. The need to pivot from one drug production to another is critical.
One of China’s largest biopharma companies was investigating ways of speeding up the movement of their chromatography columns at their plant in Wuxi. With a quick, easy coupling system the MT20-960+SS unit was the perfect fit for their operations and allowed the customer to quickly change their lab configurations with ease. Through this, they have streamlined their manufacturing process and strengthened their ability to pivot their operations.
The ongoing evolution we're seeing in biopharma industries underscores the importance of agility and strategic foresight for Asian biopharma to maintain competitiveness and meet the global demand for innovative and cost-effective healthcare solutions.
Improving production efficiency and workplace safety is key to ensuring that Asian Biopharma manufacturers remain competitive. It's vital for companies to ensure they partner with industry experts who actually understand and cater for their specific requirements to deliver a premium product that enables continued biopharma success.