Comparing AGVs to Traditional Material Handling Equipment
AGV Systems
More advanced material handling solutions, such as Automated Guided Vehicles, are kicking up a storm in the material handling industry – but how do they compare to traditional handling equipment?
Thank you for your request to download the MasterMover 'Guide to Autonomous Guided Vehicles'.
We'll also send you an email shortly with your download link included for safe keeping.
If you do not receive the email, please let us know at salesteamuk@mastermover.com.
Thank you for your request for an AGV System Consultation!
One of our representatives will be in touch with you shortly to discuss your request in more detail.
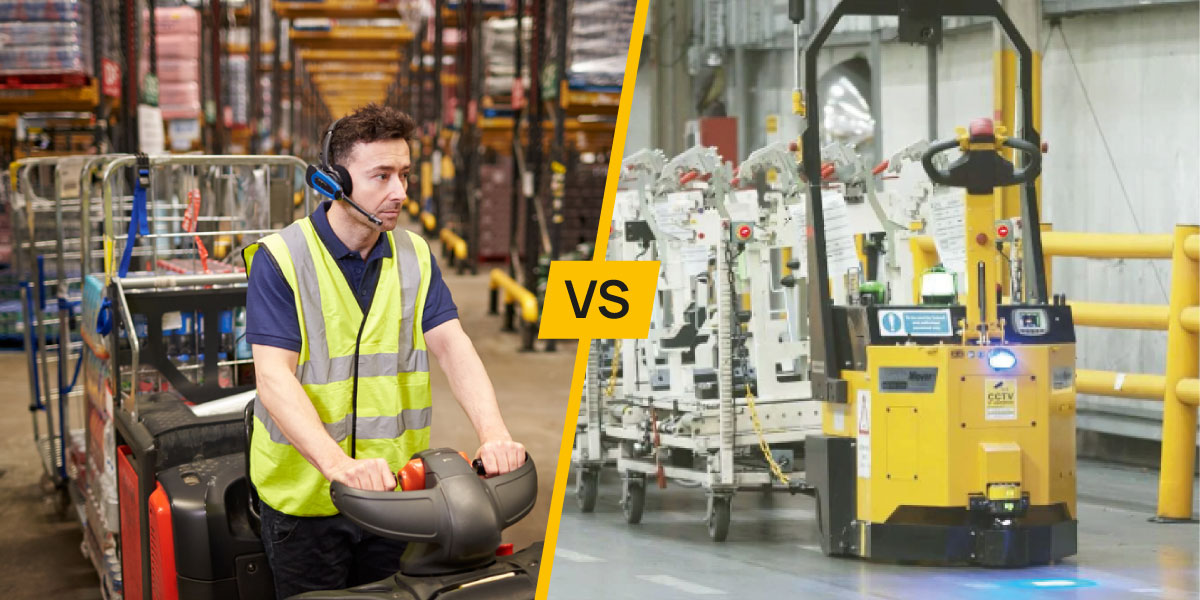
The Evolving World of Material Handling Equipment
Maximum efficiency, flexibility, and safety are three pillars every logistics warehouse and manufacturing facility strives toward. As part of this, the effectiveness of material handling processes and equipment is crucial for streamlining operations, reducing costs, and improving overall efficiency.
As the market for material handling equipment (MHE) starts to diversify to include more advanced and autonomous solutions, how do you find the right solution for your business?
We compare Automated Guided Vehicles (AGVs) and traditional material handling equipment, assessing the benefits and limitations of each. If you find yourself wondering, “Is our current material handling equipment supporting our vision?” or “Are our processes suited to automation?” then this is for you.
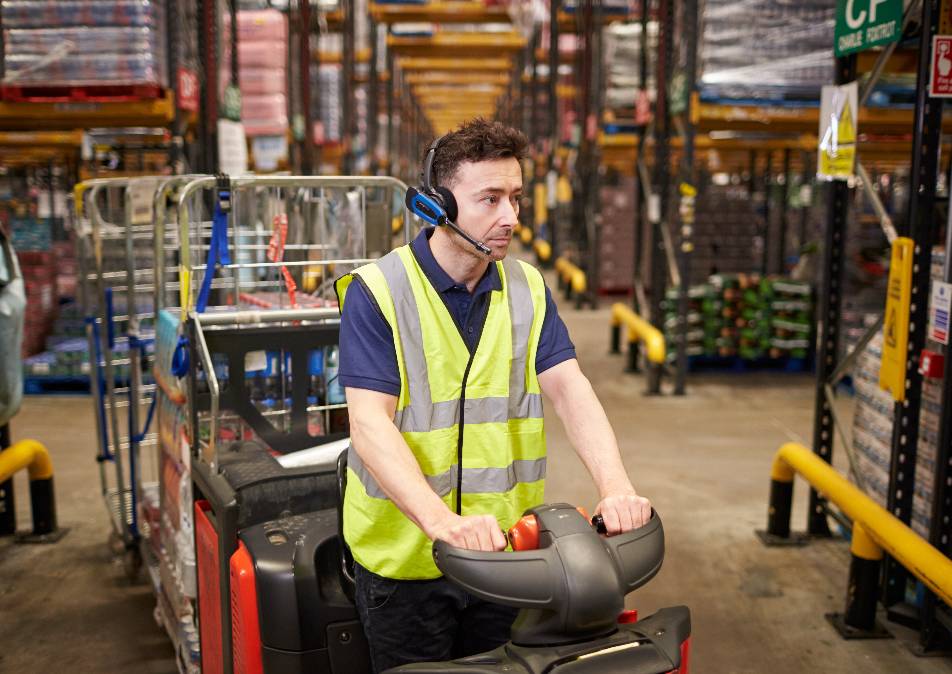
What is Traditional Material Handling Equipment?
Traditional material handling equipment includes various systems and vehicles, including forklifts, conveyors, manual carts, electric tugs, overhead cranes and more. In this context, it refers to material handling equipment that is not fitted with technology that enables it to work autonomously. Whether it’s a driven system like a forklift, a pedestrian operated electric tug or carts and trolleys -they all require the involvement of an operator.
Advantages of Traditional Equipment
Traditional handling equipment like forklifts, overhead cranes and pallet trucks are commonplace across manufacturing and logistics. Their familiarity and simplicity mean they’re used by most businesses. Despite the rise in the adoption of automation solutions, traditional handling solutions still deliver a range of benefits, including:
Ease of implementation
Standardisation of design
Versatile for a range of tasks
Lower upfront costs
Limitations of Traditional Equipment & Systems
As well as the advantages outlined above, for many businesses, traditional handling systems can also have some limitations – particularly where the movement of materials is frequent, well-defined and repetitive.
Often labour-intensive
Can be inefficient
Requires the involvement of operators
Less productive
.jpg?width=952&height=674&name=AGV_Still-1.18-Image_1200x800px%20(1).jpg)
What is an Automated Guided Vehicle (AGV)?
Automated Guided Vehicles, or AGVs, represent a more modern and advanced type of material handling equipment. These self-guided vehicles operate autonomously, removing the need for an operator by following predefined paths or routes as part of their operation.
Benefits of AGVs
Implementing AGVs delivers a range of advantages for businesses across logistics and manufacturing. More and more businesses are looking towards AGVs to drive greater operational efficiency and boost staff productivity.
Efficiency and Productivity
AGVs offer significant improvements in material handling efficiency, leading to quicker processes and reduced downtime. By eliminating the need for human involvement, AGVs free up staff to work on more productive tasks.
Accuracy
Automated Guided Vehicles deliver unrivalled accuracy in movements. Through advanced navigational technology and route mapping, AGVs deliver precise movements every time.
Enhanced Safety
AGVs are equipped with advanced safety features, minimising the risk of accidents and injuries in the workplace. By automating the movement, they also eliminate any need for manual effort.
Limitations of AGVs
Like any system or equipment, AGVs have their own limitations and are not always the right solution for every application or business.
Initial Investment
While AGVs offer long-term savings, their initial setup costs are often higher than traditional equipment.
Less Suited to Infrequent Tasks
AGVs are best suited to repetitive tasks. If processes or applications are not repetitive or are infrequent, often a more traditional handling system is more efficient.
Flexibility
The flexibility of AGVs can often be a bit of a grey area. The reality is that while AGVs can be used on a range of tasks and applications, they work to current processes.
With a manned system, an operator can use equipment as and when needed to move something quickly. Businesses that rely on their agility and quickly react to trends may not be the best fit for AGVs.
When is an AGV Right for Your Application?
-
Repetitive Material Handling
-
Predictable Environments
-
Efficiency and Productivity
-
Reliance on Manned Systems
Repetitive Material Handling
Automation, and in particular Automated Guided Vehicles, are best suited to operations that have well-defined and frequent material movements. AGVs are ideal for applications that involve the repetitive movement of materials, products, or components within a facility. They can be programmed to follow set routes and perform routine tasks consistently.
Predictable Environments
AGVs perform best in controlled and structured environments. If your facility layout is relatively consistent and well-organised, AGVs are a suitable choice.
Efficiency and Productivity
AGVs can enhance operational efficiency by reducing manual labour and transportation times. If you have a high-volume production or material handling process, AGVs can help increase productivity.
Reliance on Manned Systems
Interlinking to the areas outlined above, AGVs deliver the most significant value in operations that rely heavily on manned or driven systems. For example, if a forklift driver is spending 80% of the shift moving components from A to B – AGVs enable this to be streamlined, freeing up the driver to work on more productive tasks and reducing downtime.
Case Study – Toyota Replaces Traditional MHE with AGVs
Businesses across a range of industries are adopting AGVs as they strive towards leaner processes and greater efficiency. Discover how Toyota Motor Manufacturing leveraged MasterMover AGVs to revolutionise their material handling processes.
The ultimate guide to material handling
Material handling equipment
Looking to understand material handling in a little more detail?
We’ve compiled some helpful resources to get you started.
-
10 Principles of MHE
-
Advanced MHE
-
Best forklift trucks
-
Material handling in manufacturing
-
Forklift trucks vs electric tugs
-
Shunters vs electric tugs
-
Tow tractors vs electric tugs
-
Overhead cranes vs electric tugs
-
A fork-free future
-
What is intralogistics?
-
Diesel forklift alternatives
-
Benefits of tugger trains
Considerations for Choosing Between AGVs and Traditional Equipment
Both AGVs and traditional material handling systems have distinct advantages and limitations. As with any equipment, it’s important that you assess a range of factors to ensure you choose the right solution for your business.
Budget
Automated Guided Vehicles and other forms of automated system require a higher investment than traditional alternatives. While the benefits of efficiency typically deliver a significant return on investment, it’s important to consider the feasibility of investing in an AGV system for your business.
The initial investment is high, and for smaller operations or processes that aren’t well suited to automation difficult to justify. If the volume of your material handling processes is low and unlikely to increase significantly in the short term, you could end up investing a large chunk of capital in an unnecessary system that won’t deliver the ROI needed.
Facility Layout
As we’ve covered in this blog, AGVs are best suited to well-defined processes and layouts, delivering the highest ROI and advantages on repetitive tasks and processes.
When assessing whether you should implement an Automated Guided Vehicle into your operations, it’s important to understand the nature of your material handling processes and workflow to assess whether it would be worthwhile to automate it.
Future Plans
When implementing an AGV, it’s important to consider the future needs of the business and operation. AGVs can be reprogrammed to work on other processes or tasks, but if your operations are likely to change significantly in the near future, the last thing you want is a redundant piece of equipment.
In the ever-changing world of material handling, the choice between AGVs and traditional equipment is not one-size-fits-all. By assessing your unique needs and understanding the advantages and limitations of each approach, you can make informed decisions that will drive efficiency and success in your business.
Reliance on Manned Systems
Interlinking to the areas outlined above, AGVs deliver the most significant value in operations that rely heavily on manned or driven systems. For example, if a forklift driver is spending 80% of the shift moving components from A to B – AGVs enable this to be streamlined, freeing up the driver to work on more productive tasks and reducing downtime.
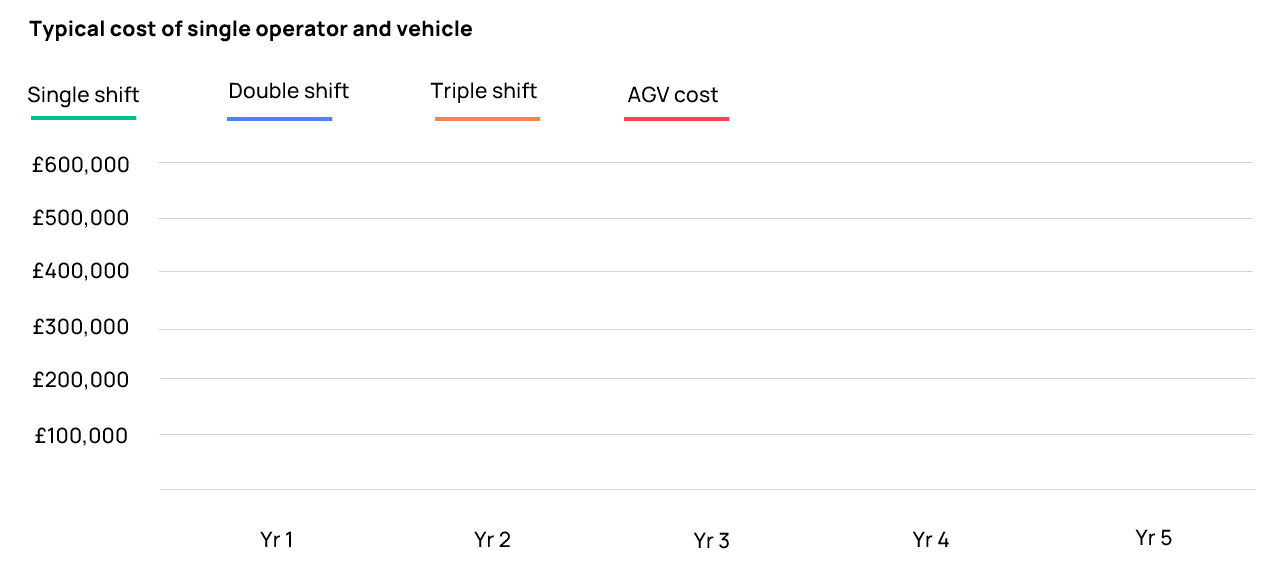
My Operation is Suited to Automation – What Return Can I Expect?
For repetitive processes, AGVs deliver an exceptional return on investment. An AGV can reach an ROI of between 50% and 150% when used on a single shift over 3 years. This can be dramatically increased to over 600% when the unit is used as part of a three-shift operation over a 5-year period.
Ready to Implement Automation in Your Business?
If you’re looking to drive repeatable, efficient movements – an AGV is the ideal solution for you. Fill in the form to discuss your AGV project with an expert.